What we did on this construction site:
- removal of old concrete;
- execution of two-layer reinforcement;
- construction of an industrial concrete floor.
How to make a high-quality industrial concrete floor for a warehouse?
Concrete floors never go out of fashion, especially in the industrial sector.
Long-term durability, ease of maintenance and recovery are just some of their advantages. Have you ever wondered how to make a high-quality industrial concrete floor for a warehouse? In this article we will try to answer this question.
The key to the process is proper planning and design of the industrial floor, which takes into account the specificity of the facility and the type of loads the surface will have to cope with. It is important that the design includes all details, such as any unevenness in places, places of the presumed greatest load, or the arrangement of pipes and ventilation ducts.
The subfloor is a key element of an industrial floor. It should be properly prepared and leveled. It is necessary to remove all remains, dirt and excess heights. Depending on the characteristics of the soil, it is recommended to install a layer of moisture insulation.
Not all polished concrete is the same. It is important to choose the right mixture that will best fulfill its tasks in the industrial space. This concerns parameters such as durability, adaptation to loads, hardness, as well as aesthetics.
The concrete mixture is evenly distributed using specialized leveling machines. They allow you to maintain the appropriate level and thickness of the industrial floor. Then the process of smoothing the surface takes place, the so-called mechanical finishing.
After pouring, the floor must harden properly. This is a process that takes from several days to several weeks, depending on the type of concrete. After this time, the floor is impregnated, this process is necessary so that there is no need to repair the floor, i.e. it is covered with special, usually polymeric agents that are intended to protect it against the influence of external factors.
After the process is completed, the industrial floor is checked to ensure that it meets certain parameters, such as strength, evenness, smoothness or water absorption.
The process of hardening industrial concrete floor is a process that should be carried out under appropriate temperature and humidity conditions. After the concrete hardens, it needs regular care to keep it in good condition for as long as possible.
Optimal results in creating an industrial concrete floor can only be achieved through proper planning, execution and quality control. Only then will the floor be not only aesthetically finished, but also durable and long-lasting like resin flooring.
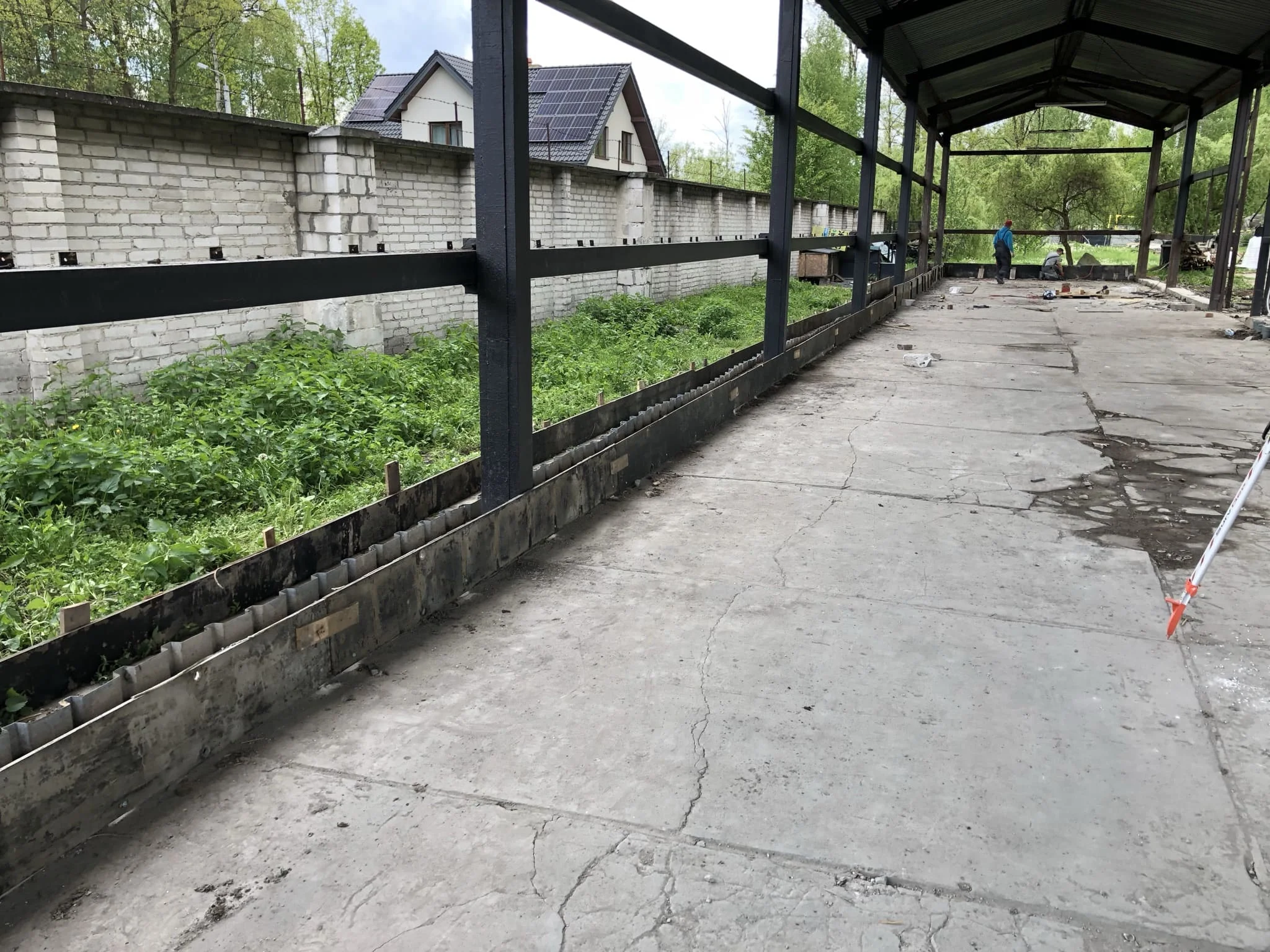
What are the equality standards for industrial concrete floors in Europe?
Evenness, durability and a properly finished surface are essential for the proper functioning of industrial concrete floors.
Standardization of these characteristics is important to ensure consistency and high quality across Europe, for both manufacturers and users. Therefore, in order to maintain quality, there are several norms and standards relating to industrial concrete floors.
Various standards and norms regulate the work with industrial concrete floors in Europe. One of them is EN 13813 "Industrial substrates and coatings - Floor performance properties", which specifies, among others, necessary mechanical characteristics, such as compressive and bending strength, as well as abrasion resistance of the floor surface.
Another relevant standard is DIN 18202 "Tolerances in buildings - Horizontal floor surfaces; maximum deviations". This German standard has been adopted at European level and serves as a guideline for determining permissible geometric deviations of surfaces, such as unevenness or deviations from horizontal.
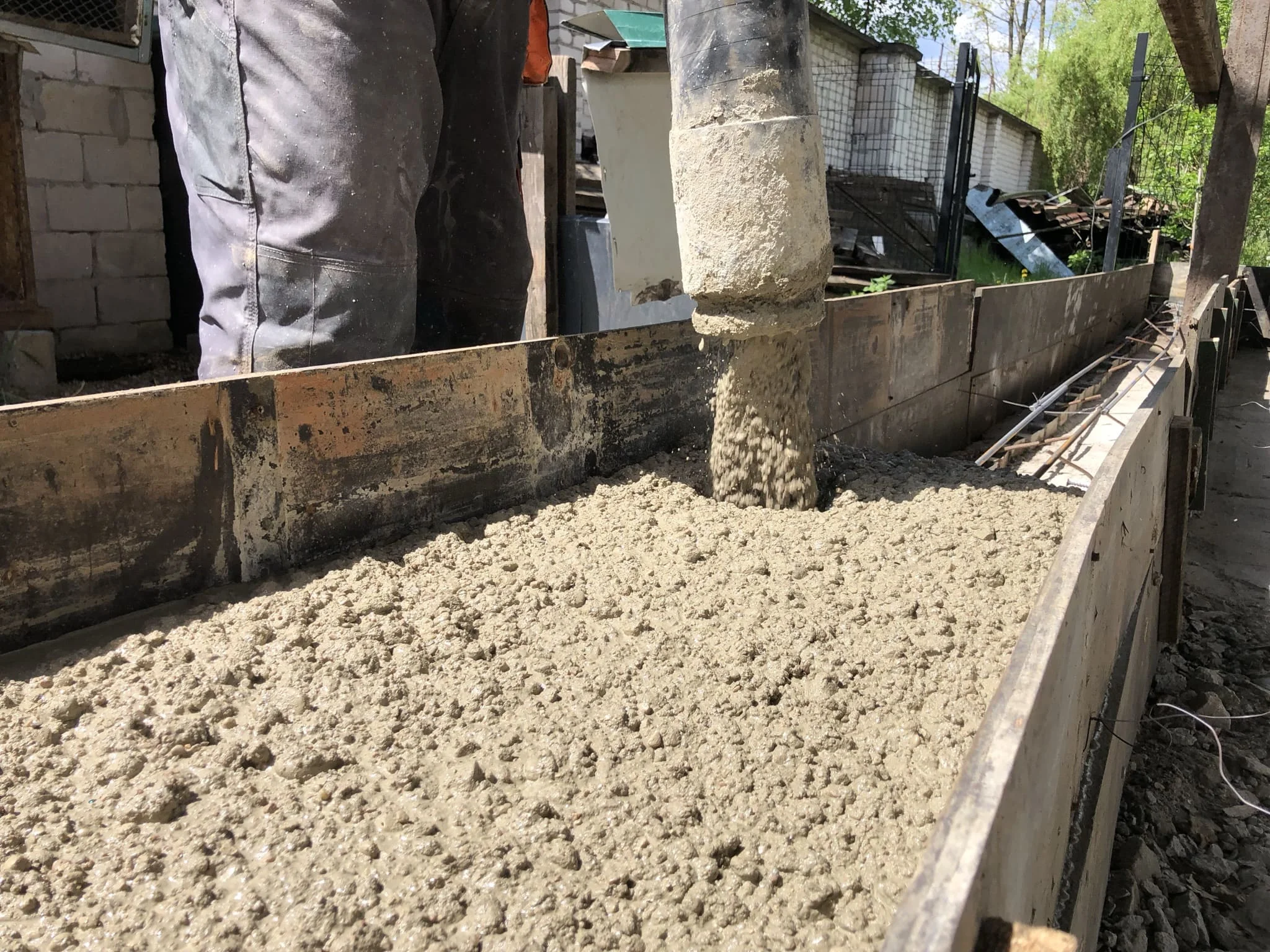
The EN 1504-4 standard offers guidance on the use of concrete for the repair of structural and non-structural industrial floors. Lists various repair methods, including techniques such as crack filling, surface repair, and waterproofing.
EN 15614, titled "Floors and surfaces for user safety and their requirements", focuses on user safety, paying particular attention to surface textures that can help prevent slips and falls. Concrete pumping is not described in any standard.
Regardless of these standards, it is important that manufacturers and contractors should ensure compliance with local building regulations and health and safety regulations such as safety barriers. Proper preparation, installation and maintenance of industrial concrete floors are crucial to ensuring long-term performance.
In summary, when it comes to industrial concrete floors, there are many standards that must be adhered to. From safety and durability standards to guidelines specifying precise dimensions and tolerances - everything to ensure that industrial concrete floors meet the expectations of customers, employees and the environment.
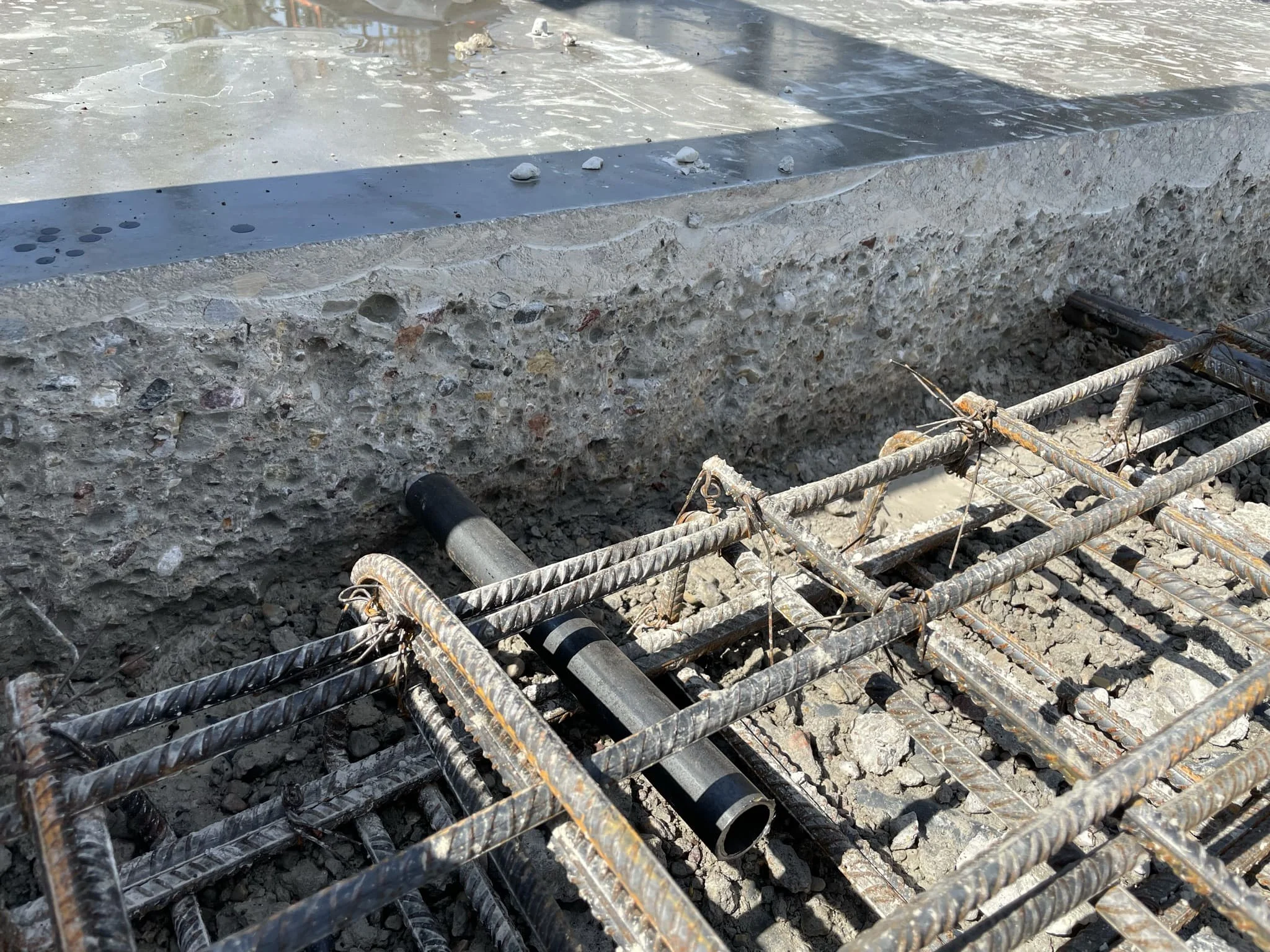
Work results:
- removal of old concrete - 120 m2;
- execution of two-layer reinforcement - 1300 m2;
- construction of an industrial concrete floor - 1300 m2.