What should be the thickness of the industrial concrete floor?
The thickness of an industrial concrete floor depends on several factors, including the expected load, the type of substrate, the operating conditions, and the site-specific requirements. Here are some general guidelines.
For floors exposed to light loads, such as pedestrian traffic or light equipment, the typical thickness of a concrete floor can be between 100 mm and 150 mm.
In the case of areas where heavier equipment, such as forklifts, is moving, or where medium-heavy goods will be presented, the industrial floor should have a thickness of about 150 mm to 200 mm.
For warehouses, production halls and other industrial environments with very heavy traffic or operations that require very durable floors, the floor thickness should be at least 200 mm to 250 mm or more. It is also important to perform polished concrete in this type of buildings.
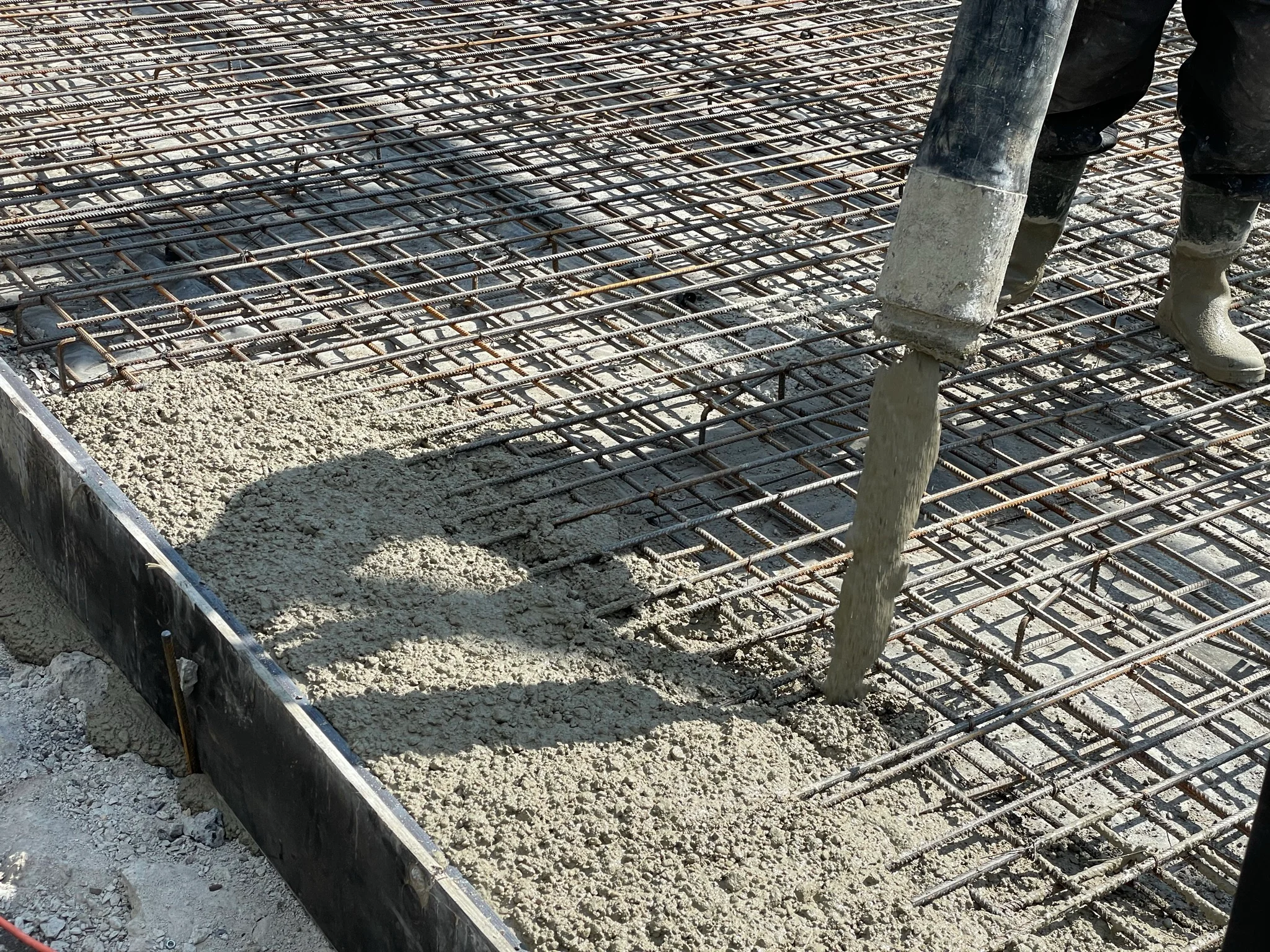
Some applications may require even greater industrial floor thickness, for example for floors designed to withstand point loads from heavy equipment or high storage racks.
It should also be taken into account the strengthening of the floor with a reinforcing mesh, polypropylene or steel fibers. These options may be necessary depending on the expected strength of the industrial floor.
When designing the thickness of industrial flooring and implementation, it is very important to consult an engineer or specialist who, based on the analysis of needs, loads and soil characteristics, will make appropriate calculations and design a floor covering that meets all the criteria of safety and strength.
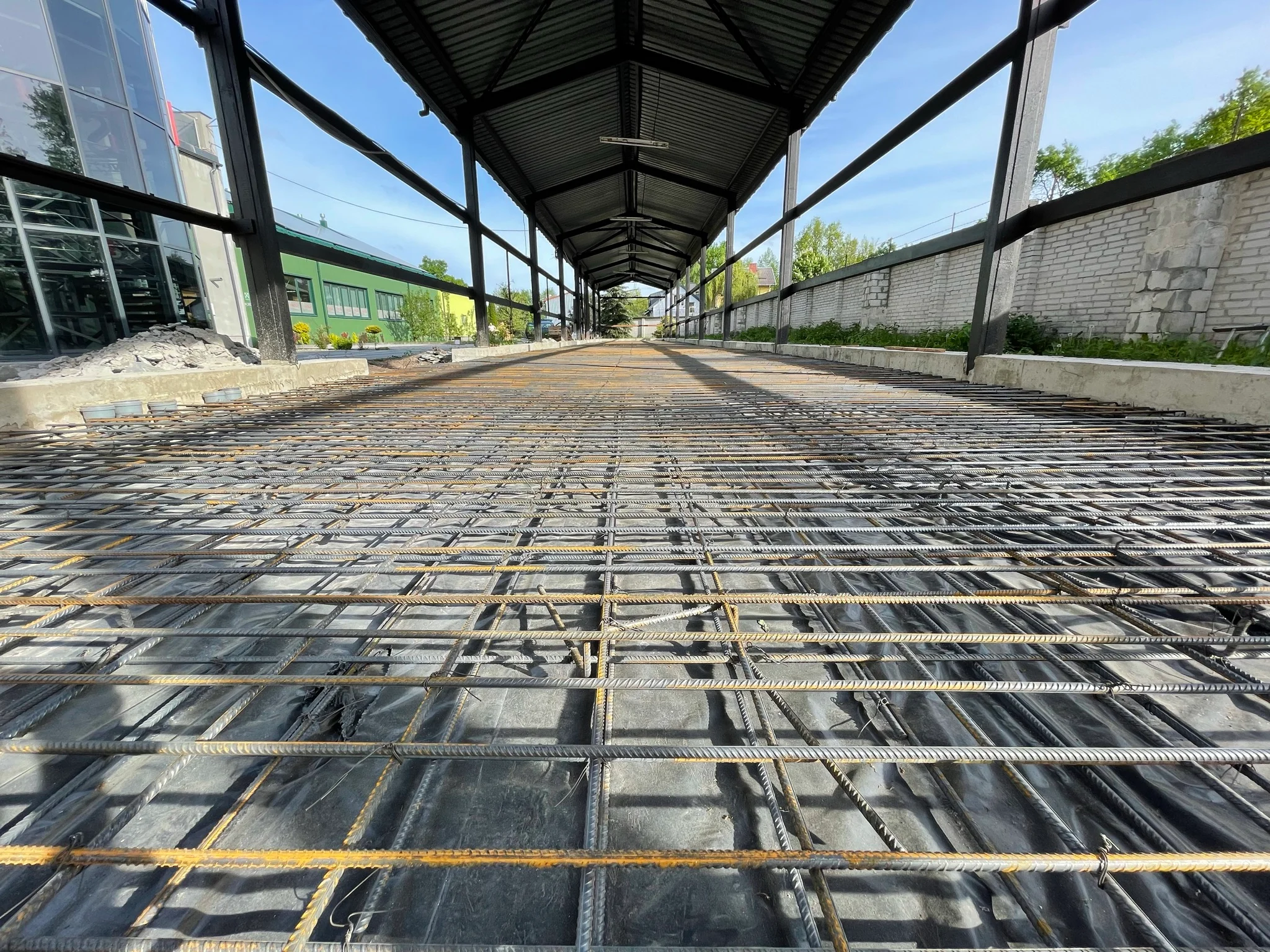
Which industrial floor to choose, concrete or polymer? How do they differ in thickness?
The choice between industrial concrete flooring and resin flooring (epoxy or polyurethane) depends mainly on the specifics of the workplace and the requirements for strength, chemical resistance, cost and aesthetics. Here are a few differences between these two types of industrial flooring.
Typically, the thickness of the industrial floor ranges from 100 mm to even 250 mm or more, depending on the load and application. Very high resistance to heavy loads and mechanical damage. The initial cost of installation may be lower than for polymer floors. Repairing concrete damage can be more complicated. Fewer finishing options.
Polymer flooring (epoxy or polyurethane) much thinner than the pouring of concrete floors, from about 2 mm to 5 mm for painting and Coating Systems, up to 6-9 mm or more for self-leveling floors, this value is very different from the thickness of industrial floors. Excellent resistance to various chemicals and substances, easy to clean, a good choice for places with strict hygiene requirements. Easier to repair than traditional concrete floors, although mechanical damage can be more common than with concrete. Choice of colors and the ability to add safety indicators, company logo, etc. The cost of material and application can be higher, but in many cases, durability and low maintenance costs can compensate for this.
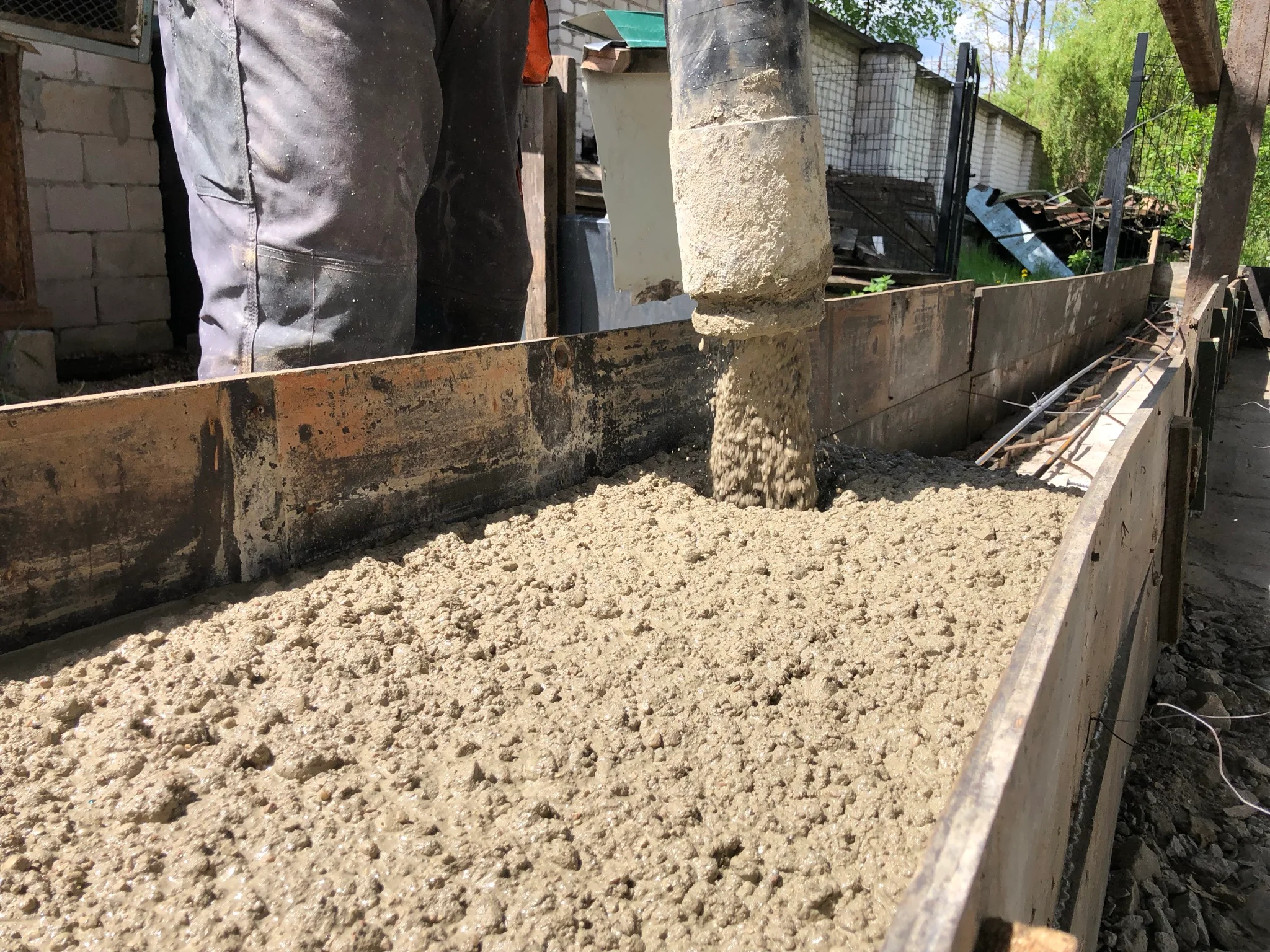
The choice between concrete and polymer flooring should be dictated by the specific needs of the place where it is to be applied. It is necessary to think about the type of activity to be carried out on the floor, the working conditions (e.g. the presence of chemicals), the aesthetics required and the budget.
Attention should also be paid to specific requirements for work safety - for example, industrial floors often have to meet strict requirements for anti-slip or fire resistance.
Regardless of the choice, it is recommended to consult a professional or a company specializing in industrial flooring, which will help to adjust the best solution to the specific conditions and thicknessand industrial flooring.