What we did on this construction:
- ground grinding;
- strengthening of the entrance edge;
- repair of cracks;
- making plinths;
- making a floor of epoxy resin.
Choice of resin flooring. What is the difference between epoxy and polyurethane resin?
Epoxy and polyurethane resins are two of the most commonly used materials in many industries, they are the two main materials we use for resin flooring. Both provide robust, durable and efficient solutions, but they also have their own unique characteristics, which makes them better for use in a variety of situations. Here are a few key differences between these two types of resins.
Strength and hardness: Industrial floors are made of epoxy resin. Epoxy resins are generally harder and have higher pressure strength than polyurethane resins. For this reason, they are usually preferred in places that require high strength, such as industrial floors or aircraft structures.
Temperature resistance: Epoxy Resins usually have better resistance to high temperatures. On the other hand, polyurethane resins are more resistant to low temperatures, making them an ideal choice for outdoor applications in cool climates.
Flexibility: Polyurethane resins are definitely more flexible than epoxy resins, which makes them better suited to areas that deal with temperature fluctuations or vibrations.
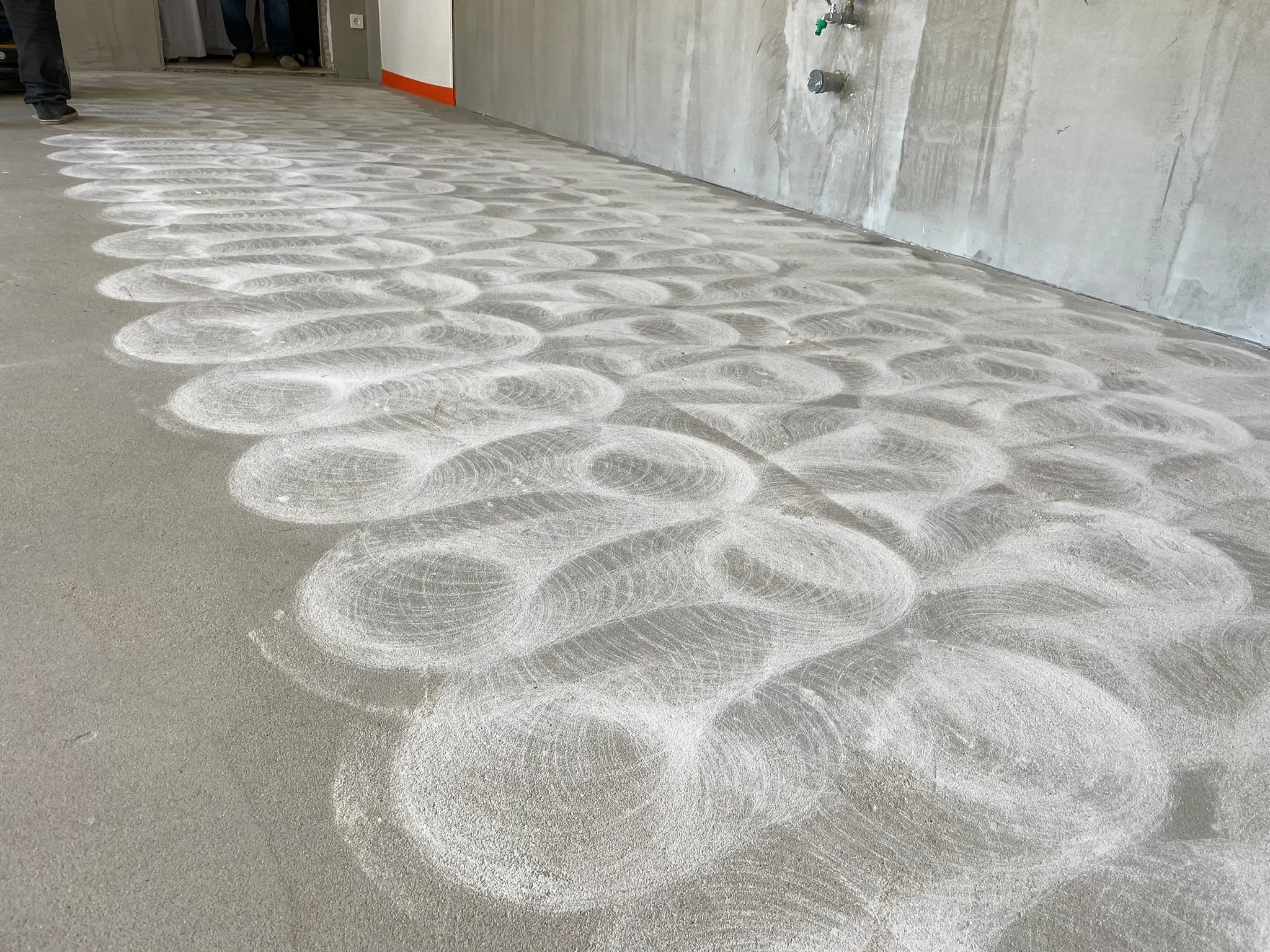
UV resistance: Polyurethane resins are generally more UV resistant, which means they do not turn yellow or become brittle under direct sunlight.
Drying time: Epoxy Resins typically take more time to dry and Harden compared to polyurethane resins, which reduces their value in terms of speed of work.
Durability: Although epoxy resin is characterized as very durable, polyurethane resin is usually more resistant to abrasion, fatigue of the material and the effects of various chemicals.
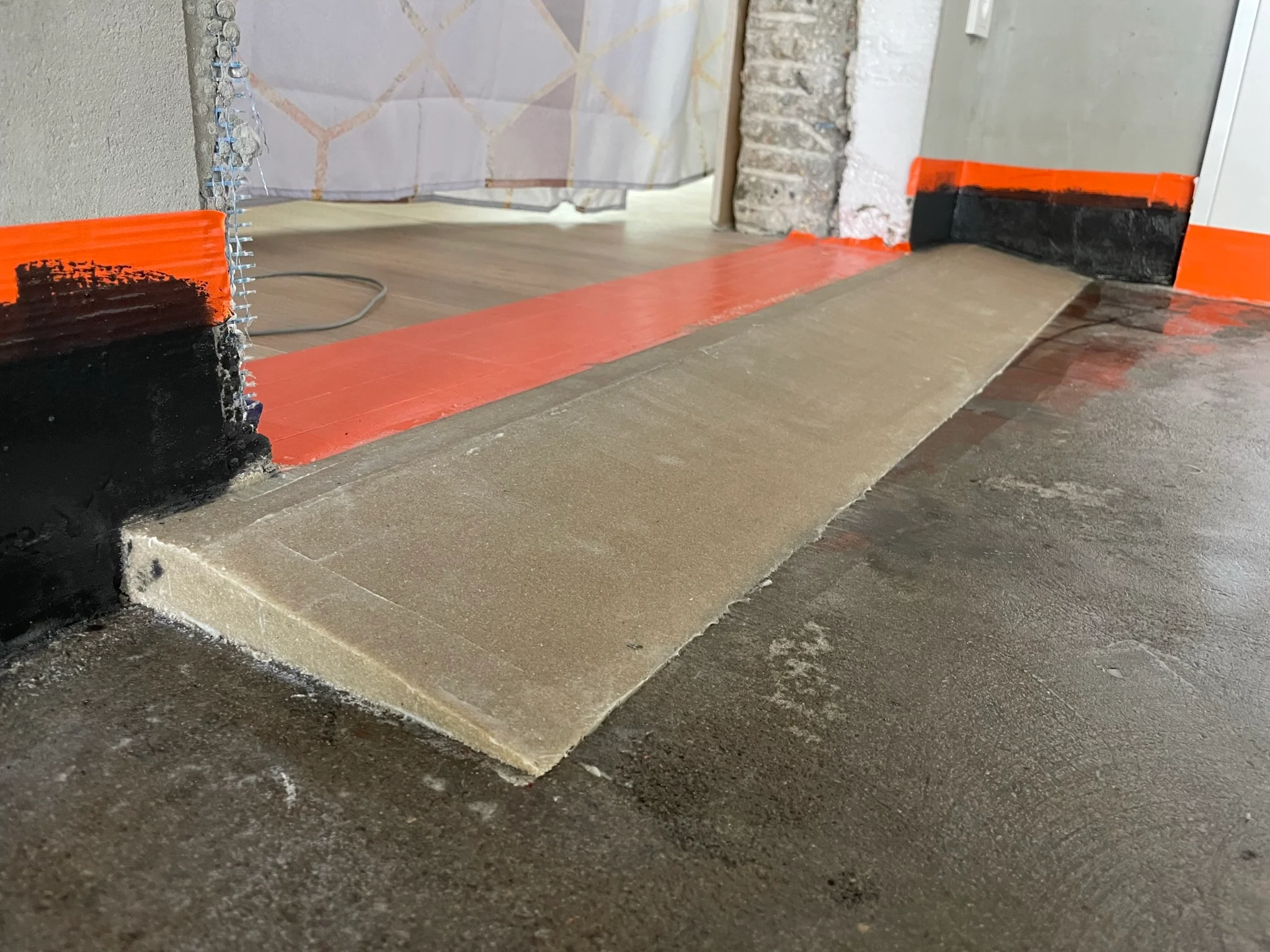
Application: Due to the difference in characteristics, epoxy resin is usually used in areas where high strength and hardness are required, such as resin floors, while polyurethane resins perform better in places that require greater flexibility and resistance to weather conditions.
In summary, both epoxy and polyurethane resin have their own unique advantages and applications. The choice between these two materials depends on the specific requirements of the project.
How is epoxy resin made for resin floors?
Epoxy resin is a two-component, useful material used in various fields such as construction, automotive, aerospace and others.
Used for making industrial floors, creating unique furniture, laminating, casting and protecting surfaces from moisture and chemicals, epoxy resin is an indispensable element in many technological processes. But how is this versatile material really made? Let's do a deep dive. To begin with, you need to understand that epoxy resin is formed by a chemical reaction of two components: the epoxy resin itself and the hardener. These two components are mixed together, which causes a reaction that leads to the formation of a solid material - a ready-made epoxy resin.
The first element is epoxy resin, which is used for resin flooring, which is an organic compound containing epoxy groups (that is, oxygen and carbon atoms). These resins are produced industrially mainly from epihalohydrins and bisphenol A. The Epihalohydrins that are used to make the resins are organic chemical compounds that contain the reactive halogenated epoxy group. The most commonly used epihalohydrin is epichlorohydrin, which is made from propylene, which is a byproduct of petroleum refining.
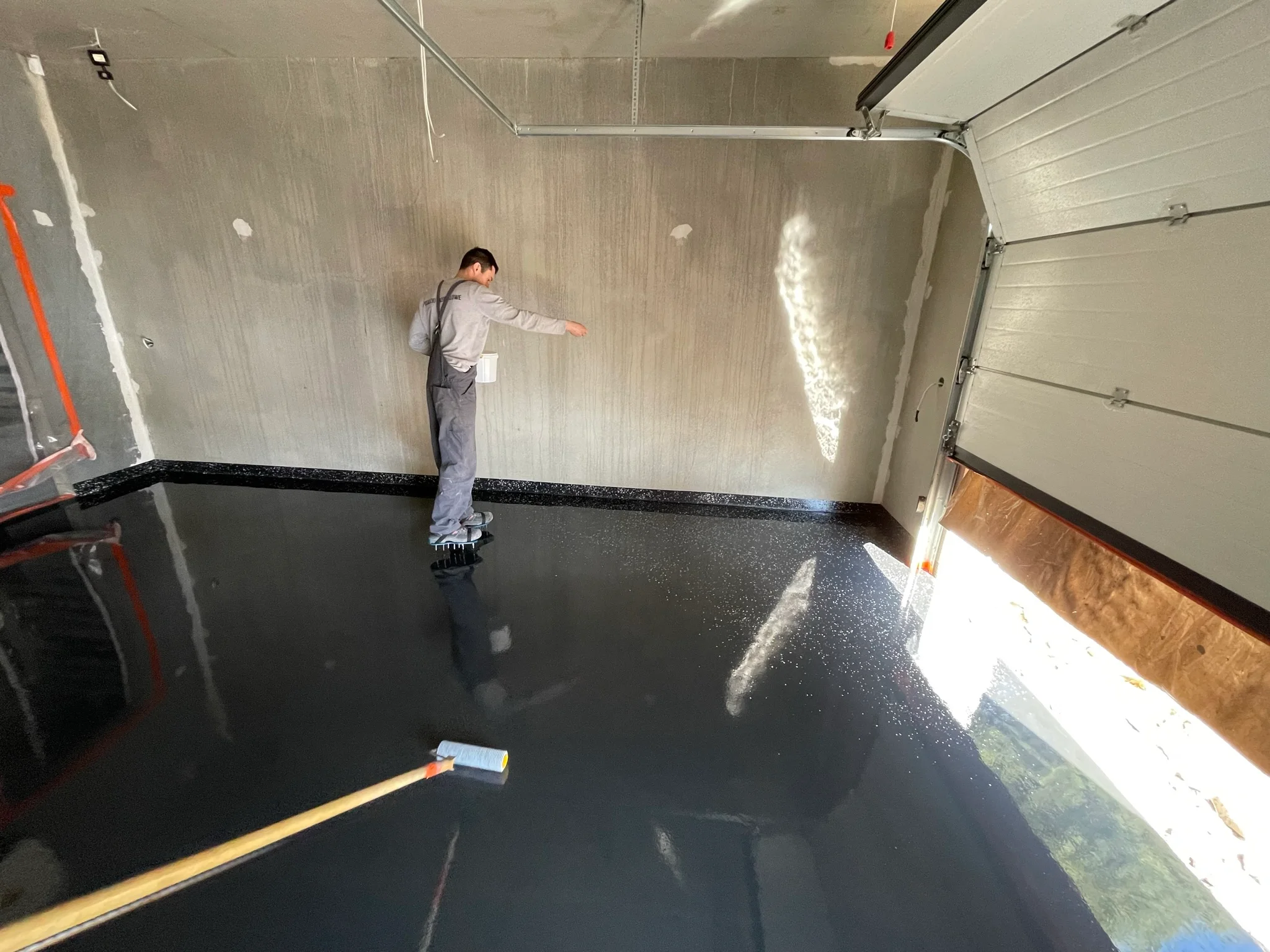
Bisphenol A is another key ingredient needed to produce epoxy resin. It is an organic synthetic compound that is widely used for the production of polymers. Bisphenol A is produced by condensing two phenol equivalents with one acetate equivalent. When epihalohydrin is combined with bisphenol A, a resin is formed. The mixed substance is then subjected to a repeated distillation, filtration and cleaning process, resulting in an industrial-grade epoxy resin.
The second component of epoxy resins for resin floors is a hardener. Hardeners can be based on many different chemicals, depending on the expected properties of the final product, such as high temperature resistance, weather resistance, flexibility and others. Hardeners bind chemically to the resin, allowing it to pass from liquid to solid form. One of the most important steps in the process of epoxy resin formation is the thorough mixing of the ingredients. The ingredients must be well mixed to ensure the uniformity of the final product. In summary, the epoxy resin production process is a precise and complex chemical process that requires both expertise and thorough quality control. The product offers exceptional strength, durability and versatility, which makes epoxy resin irreplaceable in many industries.
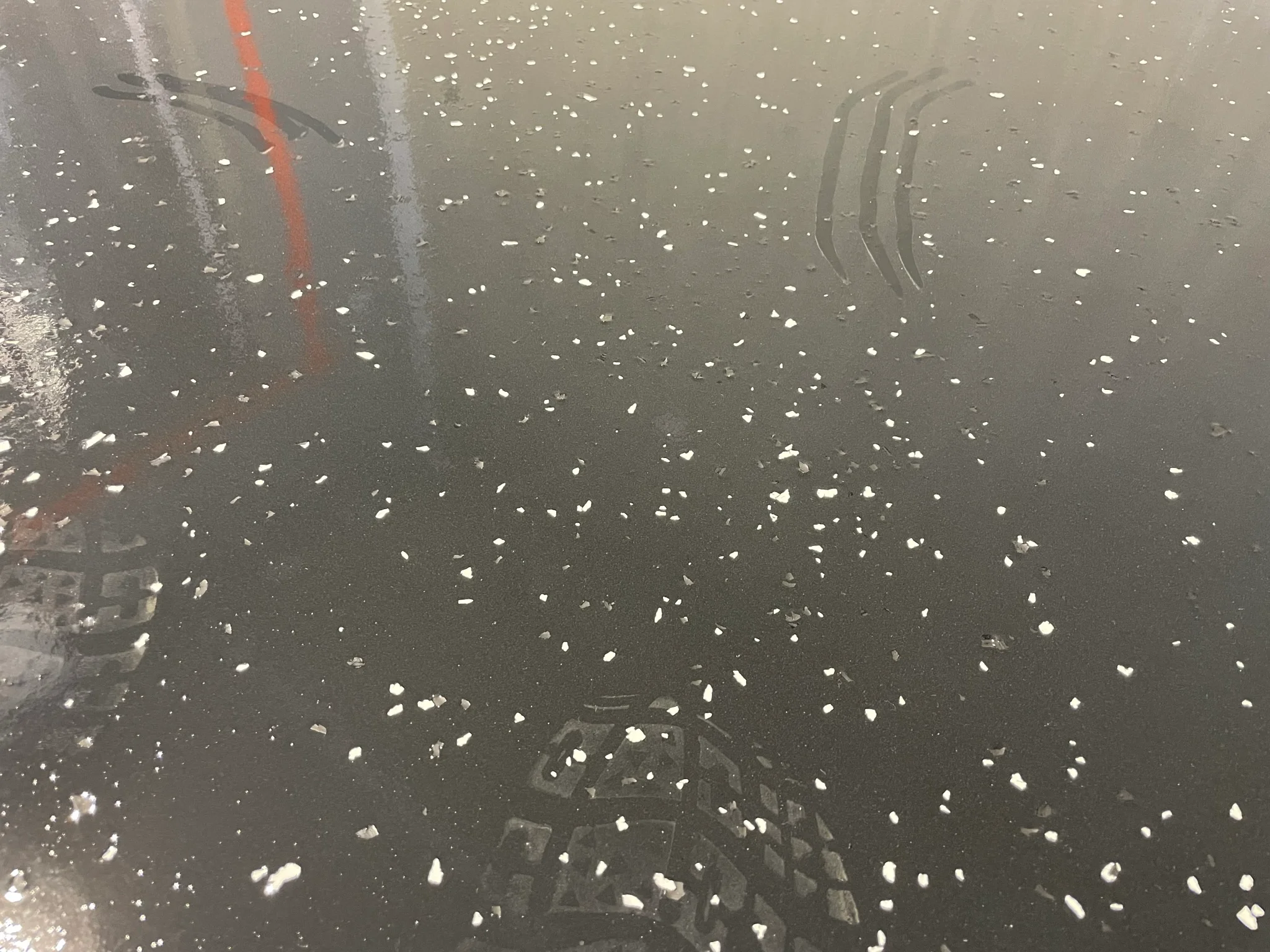
Results of work:
- ground grinding - 50 m2;
- strengthening of the entrance edge - 6 lin.m;
- repair of cracks - 4 lin.m;
- making plinths - 20 lin.m;
- making a resin floor of epoxy - 50 m2.