What we accomplished on this site:
- execution of an industrial concrete floor without subsequent smoothing;
- dilation cutting.
Report on the execution of a concrete floor in the hospital kitchen.
Last year, our company had the opportunity to undertake a challenging yet extremely satisfying task – creating an industrial concrete floor in a hospital kitchen. The project was ambitious and required not only high precision but also excellent team organization.
Our seven-member team consisted of experienced professionals who were well-versed in their trade. We knew we had a massive amount of work to accomplish in just two days. From Warsaw, we had to travel a distance of 400 kilometers to reach the site. Our schedule was tight, and every minute counted.
The hospital kitchen where we had to work was filled with challenges. One of the most significant was the large number of pipes and installations that needed to be carefully considered during the planning and execution of the industrial concrete floor. In such conditions, any mistake could lead to serious problems that could affect the operation of the entire hospital.
On the first day, we brought the pump and all necessary tools to the site. We started by repairing the floors and pouring the concrete, making sure to distribute the material evenly. It was crucial that the concrete filled every nook and cranny, especially around the installations. This required great precision and collaboration from the entire team. Without the possibility of subsequent smoothing, we could spot any shortcomings during the work itself.
On the second day, it was time for dilation cutting of the industrial concrete floor. This stage was particularly difficult, requiring precise measurement and meticulous work. Dilation joints are crucial to prevent concrete cracking due to shrinkage and expansion from temperature and humidity changes. However, in the demanding conditions we encountered at the site, accomplishing this task proved to be quite a challenge. We worked continuously to cut the appropriate gaps that would allow the concrete floor to function properly for years.
Although the work was challenging and required great dedication and precision, the results were worth it. We managed to create the floor without subsequent smoothing, which was a key goal of this project. The final result surprised not only us but also the hospital management – the floor was perfectly uniform and met all quality standards.
The execution of the industrial concrete floor in the hospital kitchen was one of the most demanding projects we had the opportunity to carry out. Thanks to excellent cooperation, solid skills of our team, and proper planning, we managed to meet the challenge. The effort paid off, and we could complete the project with pride, knowing that we contributed to improving the hospital's infrastructure quality.
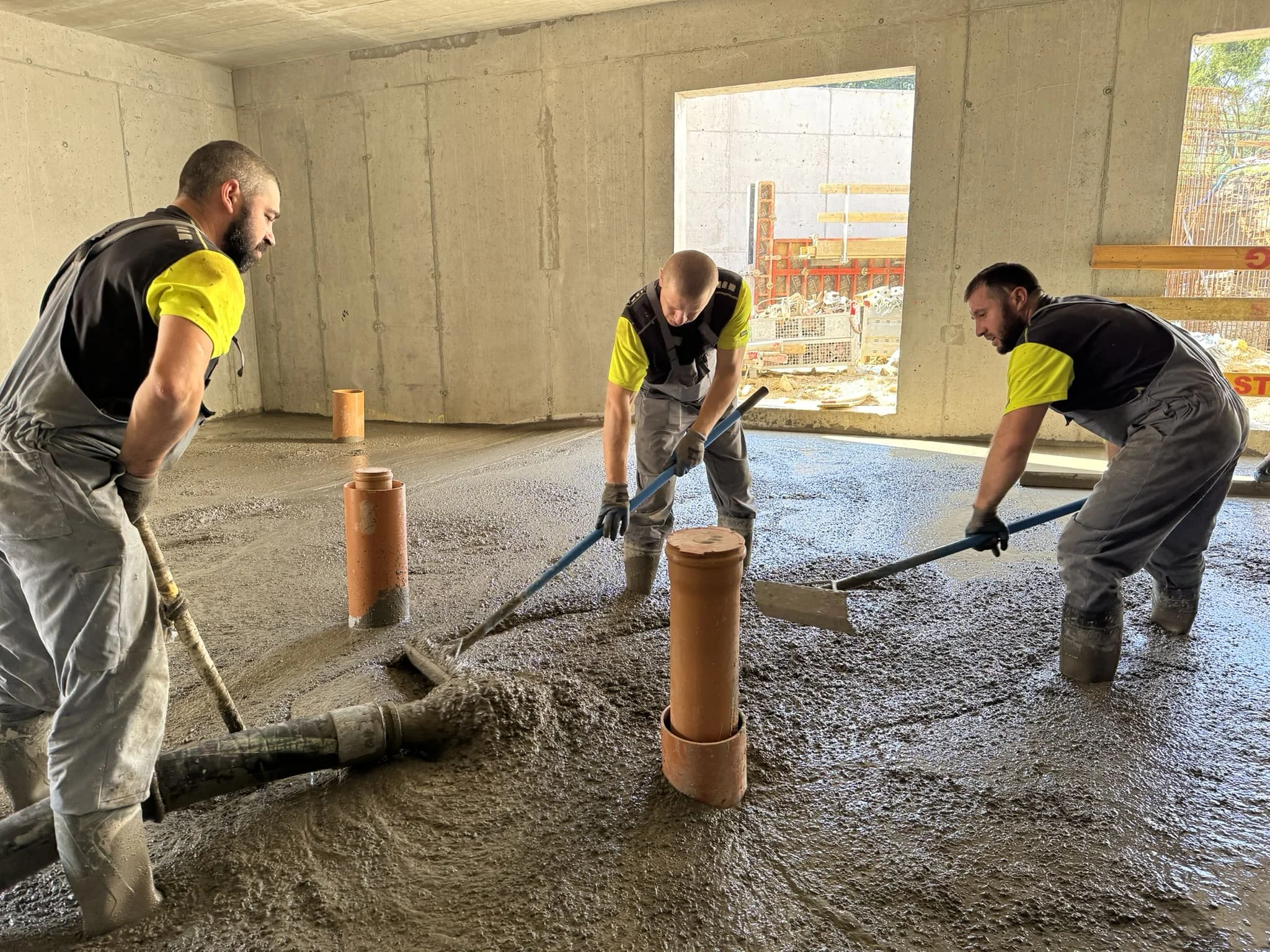
Requirements for the construction of a substructure with an industrial concrete floor in hospitals.
Requirements for the construction of a substructure with an industrial concrete floor in hospitals.
In hospitals, one of the key infrastructure elements is the industrial concrete floors in industrial areas such as kitchens, laundries, laboratories, or technical spaces. Ensuring their durability and meeting all stringent sanitary requirements is essential to guarantee the safety of patients and staff. Here are the detailed requirements for the construction of a substructure with an industrial concrete floor in hospitals.
Polished concrete used for industrial floors in hospitals should have adequate strength, typically at least class C25/30. Depending on the mechanical loads and use specifics, it may be necessary to use concrete with higher strength parameters.
Industrial concrete floors in hospitals must be resistant to intensive use and various chemical substances that can affect their structure. Therefore, it is recommended to use special concrete mixes and chemical additives that increase resistance to abrasion and aggressive cleaning agents.
The substrate on which the industrial concrete floor will be laid must be stable and have adequate load-bearing capacity. Before starting the work, geotechnical investigations should be conducted to ensure that the substrate meets technical requirements. If necessary, initial substrate stabilization can be used, e.g., with a layer of cement-stabilized aggregate.
The substrate must be dry and properly prepared for drainage before pouring the concrete. The moisture content of the substrate should not exceed 5% to avoid adhesion problems and the risk of cracking.
A sub-base layer of aggregate with appropriate granulation is often used under the industrial concrete floor, ensuring even load distribution and improving thermal insulation. The thickness of the layer depends on the load specifics and soil conditions, but it usually ranges from 15-20 cm.
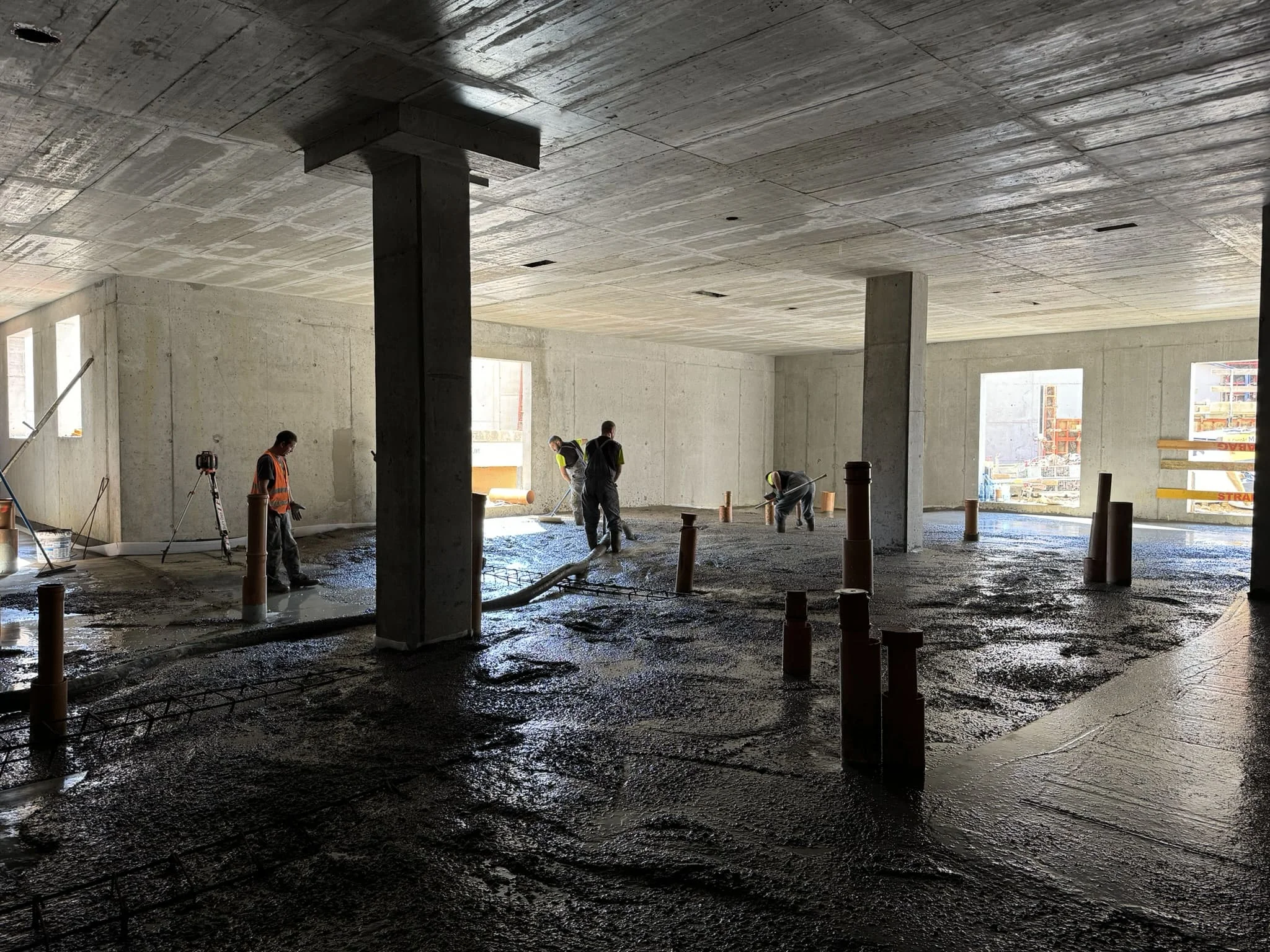
Hydroisolation is critical for hospital concrete floors. An effective water barrier prevents moisture from penetrating the concrete, protecting the structure from damage. Depending on the area specifics, waterproofing films, bituminous membranes, or special hydrophobic coatings can be used before starting to pump concrete.
Floors exposed to heavy loads should be properly reinforced. Steel meshes or polypropylene fibers are usually used, which increase tensile strength and crack resistance. It is important for the reinforcement to be properly fixed and anchored.
To achieve a uniform and smooth surface, the industrial concrete floor should be poured evenly and then carefully smoothed. In hospitals, especially in areas with high sanitary requirements, it is important that the surface is smooth and easy to keep clean.
In industrial floors, dilation joints are necessary to prevent concrete cracking at natural stress points. Dilation cutting should be done at the appropriate time after pouring the concrete and to the correct depth, according to the technical design.
After drying and hardening the industrial concrete floor, it is worth applying protective coatings, such as epoxy resin floors, polyurethanes, or special impregnations. These coatings not only increase the mechanical resistance of the concrete but also protect it from chemicals and make it easier to maintain hygiene.
To ensure that the concrete floor retains its properties for a long time, regular maintenance is necessary. Technical inspections and repairs of any damage should be carried out according to the recommendations of the concrete manufacturer and building standards. To achieve safety standards, new industrial floors must be installed with safety barriers.
The construction of a substructure with an industrial concrete floor in hospitals requires careful attention and adherence to numerous material quality and execution technique standards and guidelines. Key importance lies in the proper preparation of the substrate, the choice of appropriate concrete, professional execution of construction layers, and the application of protective coatings. Thanks to this, the concrete floor will be durable, robust, and meet the strict sanitary requirements set by hospitals.
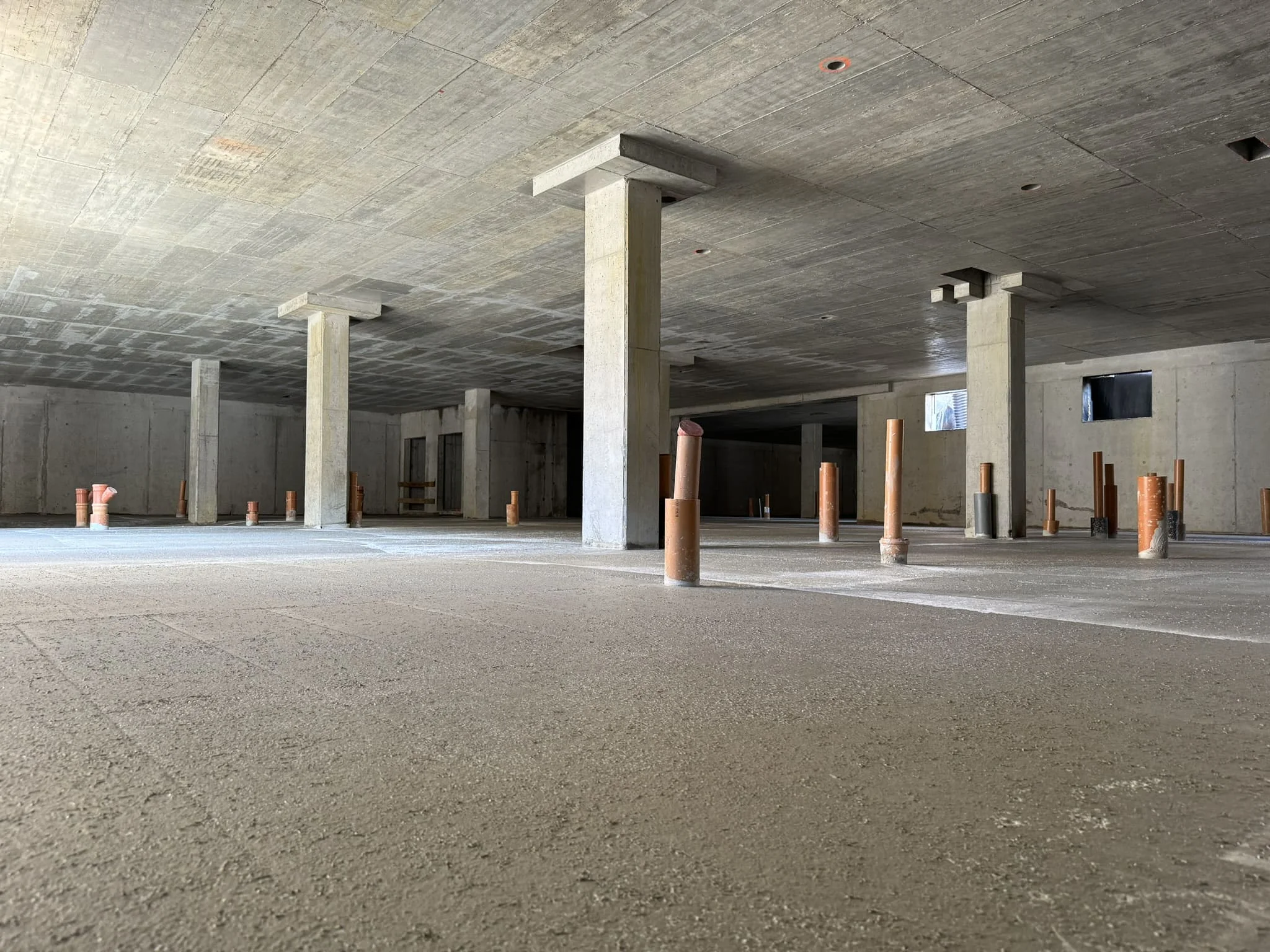
Work results:
- execution of an industrial concrete floor - 2350 m2;
- dilation cutting - 760 lm.