Anti-slip epoxy floor: Combining safety with functionality.
Anti-slip epoxy flooring is a specialized type of floor covering made of materials based on epoxy resins.
Epoxy is a type of synthetic resin that is used to create strong, durable and wear-resistant surfaces. Adding additives such as quartz sand or specialized anti-slip granules makes them suitable for places where there is a risk of slipping.
The need for anti-slip properties is primarily created by the environment in which the floor will be used. This protection is intended to increase safety, e.g. in places with high humidity, where slipping may occur, or in places where spilled substances, such as oils or chemicals, are common.
A standard epoxy floor may be smooth and shiny, which, although aesthetically pleasing, may pose a slip hazard. That is why anti-slip epoxy floors are used, which, despite retaining other positive properties of epoxy floors (such as resistance to chemicals, easy to clean, and high durability), also offer increased safety of use.
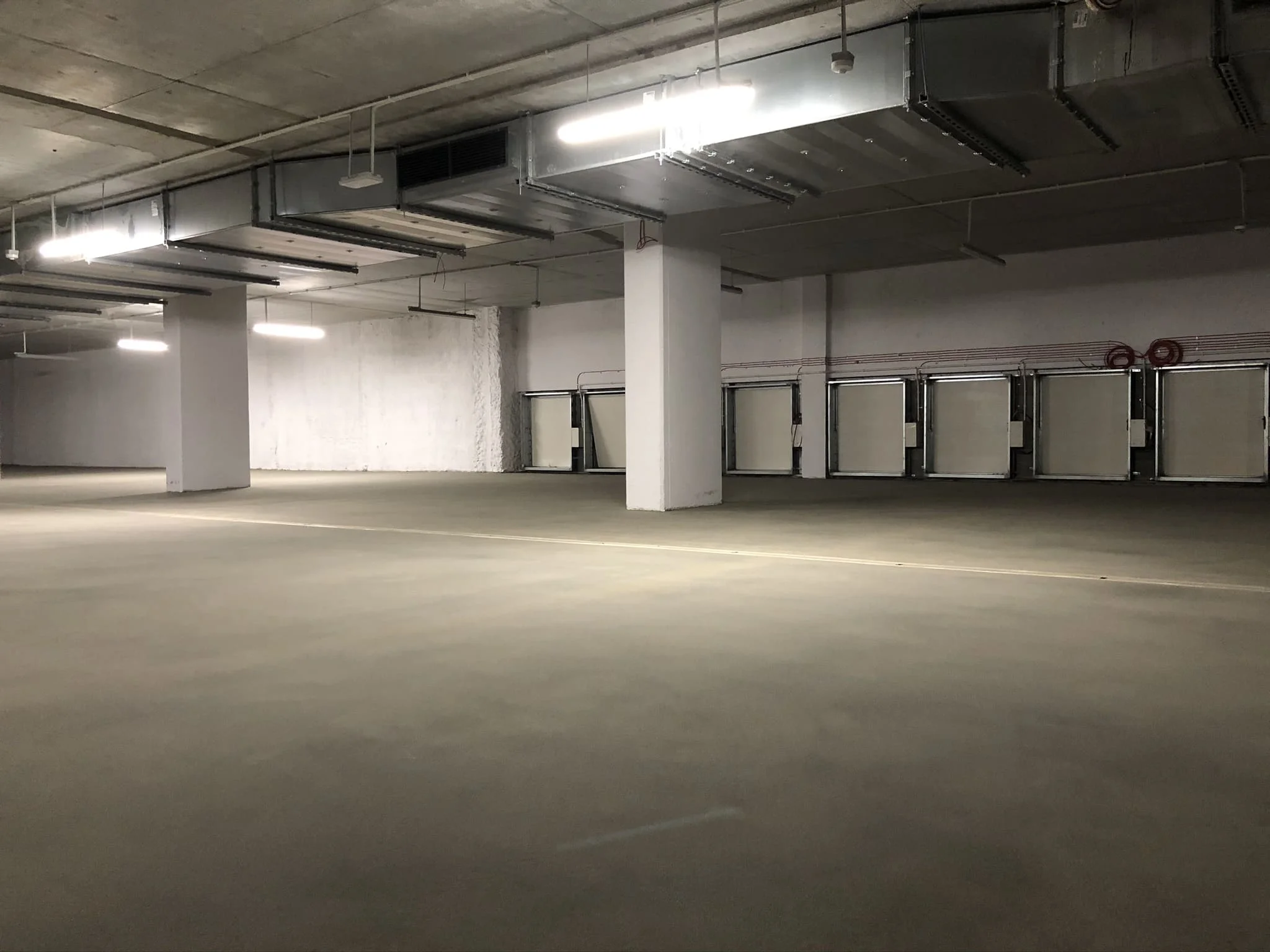
How to make an anti-slip epoxy floor?
Installing an anti-slip epoxy floor requires careful preparation of the surface and the skills of a professional contractor.
A key factor in the installation process of anti-slip epoxy flooring is surface preparation. This process usually requires cleaning and sanding the existing surface, which allows for better adhesion of the epoxy resin. Professional installers use a variety of tools, such as grinders and pressure washers, to ensure that the subfloor is clean and free from any type of contaminants.
Then, the epoxy resin should be thoroughly mixed with the hardener. It is important to follow the manufacturer's recommended proportions to achieve optimal results. After mixing the ingredients, the resulting mixture is applied to the prepared surface using a roller or brush. The key is to apply the resin evenly, avoiding lumps or blisters.
The final stage of the process involves applying anti-slip granules. The granulate is poured onto the still unset epoxy resin, allowing it to reach all places. After the epoxy dries, the surface is covered with a transparent layer of epoxy to seal everything and fix the granules on the surface. This detailed process is divided into the following stages:
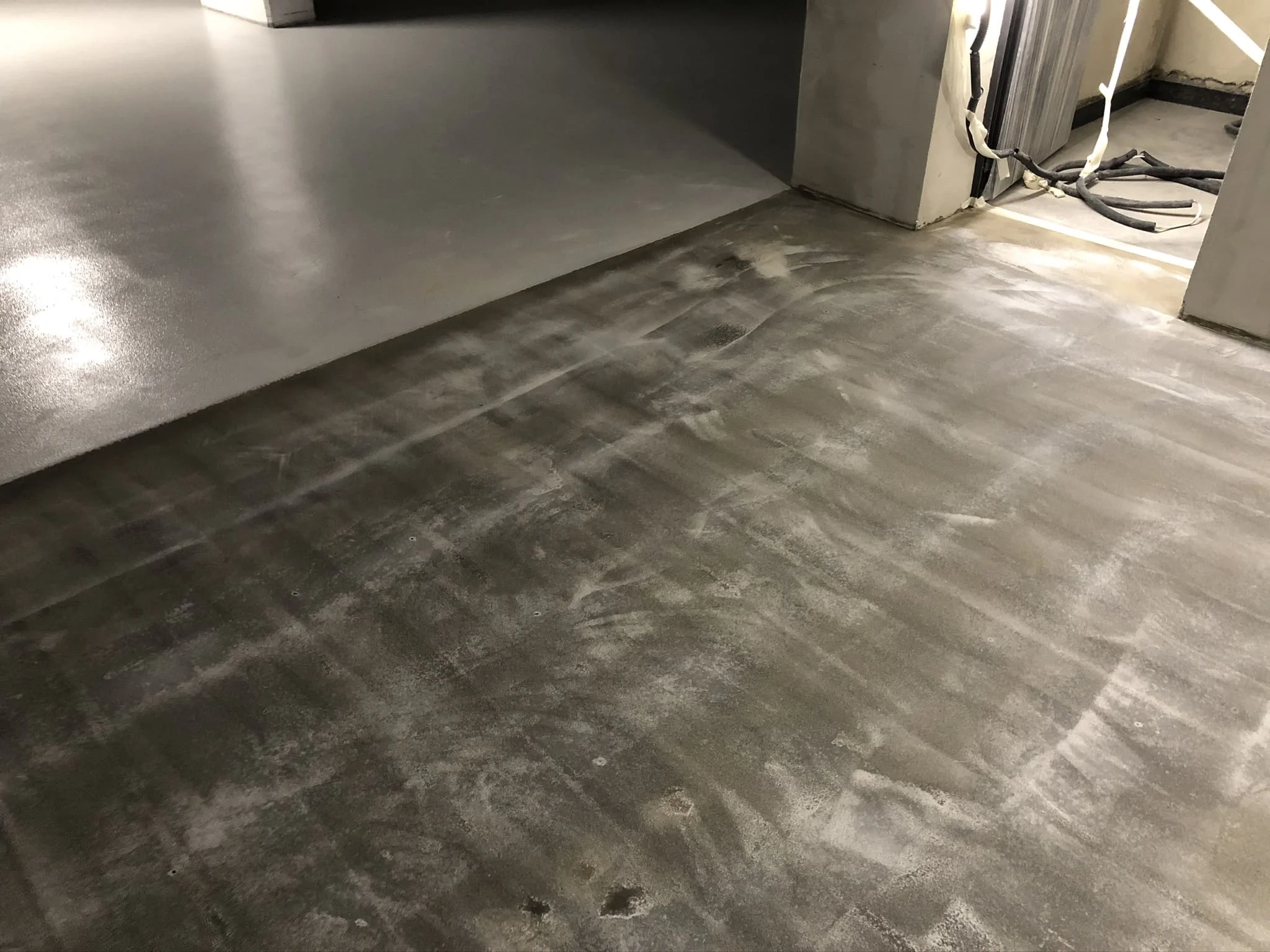
1. Preparation of the substrate: First, remove all types of contamination, such as oil, grease or dust. The substrate must be even and stable, so it may be necessary to level out any unevenness by grinding or milling. Removing old coatings ensures better adhesion of the new floor. There is often a need to repair the floor before starting to lay the resin.
2. Priming the substrate: A priming layer is applied, which increases the adhesion of the floor and prevents the formation of air bubbles.
3. Applying the epoxy layer: The epoxy resin components are mixed according to the manufacturer's instructions. The mixture is then spread evenly on the substrate.
4. Adding anti-slip elements: In order to obtain anti-slip properties, a special agent is poured into the still wet epoxy resin, such as quartz, quartz sand, or corundum. It is important that the grains are evenly distributed.
5. Finishing with a sealing layer: The final stage is to apply a sealing layer that will protect the topping and add shine to the industrial floor, and at the same time make it easier to clean.
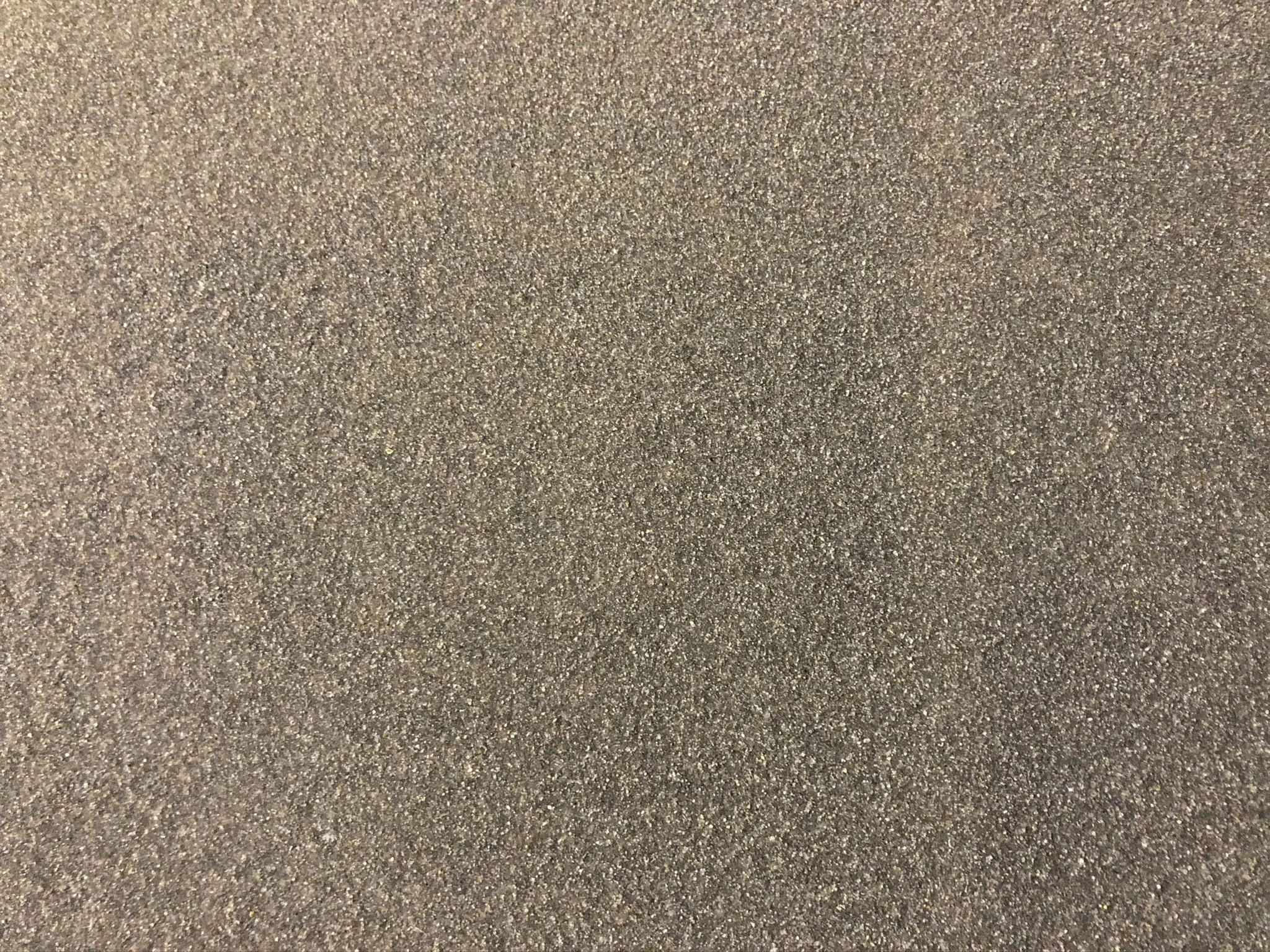
Where is this type of flooring used?
Anti-slip epoxy flooring is used in many areas that have high foot traffic and require a high level of safety.
They are often used in places such as warehouses, shops, parking lots, workshops, hospitals, laboratories, swimming pools, fitness centers, and even in industrial premises that are exposed to contact with oils or chemicals.
These floors are also often used in home spaces, such as garages, basements or utility rooms. Thanks to their anti-slip properties and ease of cleaning, they are an excellent choice for those who are looking for a functional and aesthetic solution.
Finally, anti-slip epoxy floors are popular in public places such as movie theaters, schools and shopping malls, where durability and safety are top priorities.
To sum up, anti-slip epoxy flooring is a universal solution that can be used in a wide range of places and spaces. Thanks to its unique properties such as durability, aesthetics and safety, it is an excellent alternative to traditional types of concrete floors, for example as polished concrete floor. However, for best results, installation should be carried out by experienced professionals.