Polished concrete floor for warehouse and production
Why has this type of industrial floor become so popular?
Polished concrete floor for warehouse and production is a solution that has gained wide recognition in the industrial and commercial sectors. In most cases, when we talk about superior quality, durability and cost effectiveness, the industry chooses polished concrete floors. But why?
Concrete is an extremely durable material that becomes even more durable after polishing. The main reason why companies choose polished concrete floor is its incredible durability. Concrete floors are resistant to heavy traffic, impacts and the weight of large machines and vehicles. This is extremely important in places such as warehouses and production halls, where the floor is constantly used.
In addition to their unrivaled durability, polished concrete floors are extremely easy to maintain. Polishing creates a smooth surface that is easy to keep clean - just use a regular cleaning machine or a mop. With regular cleaning, a polished concrete floor can look like new for many years.
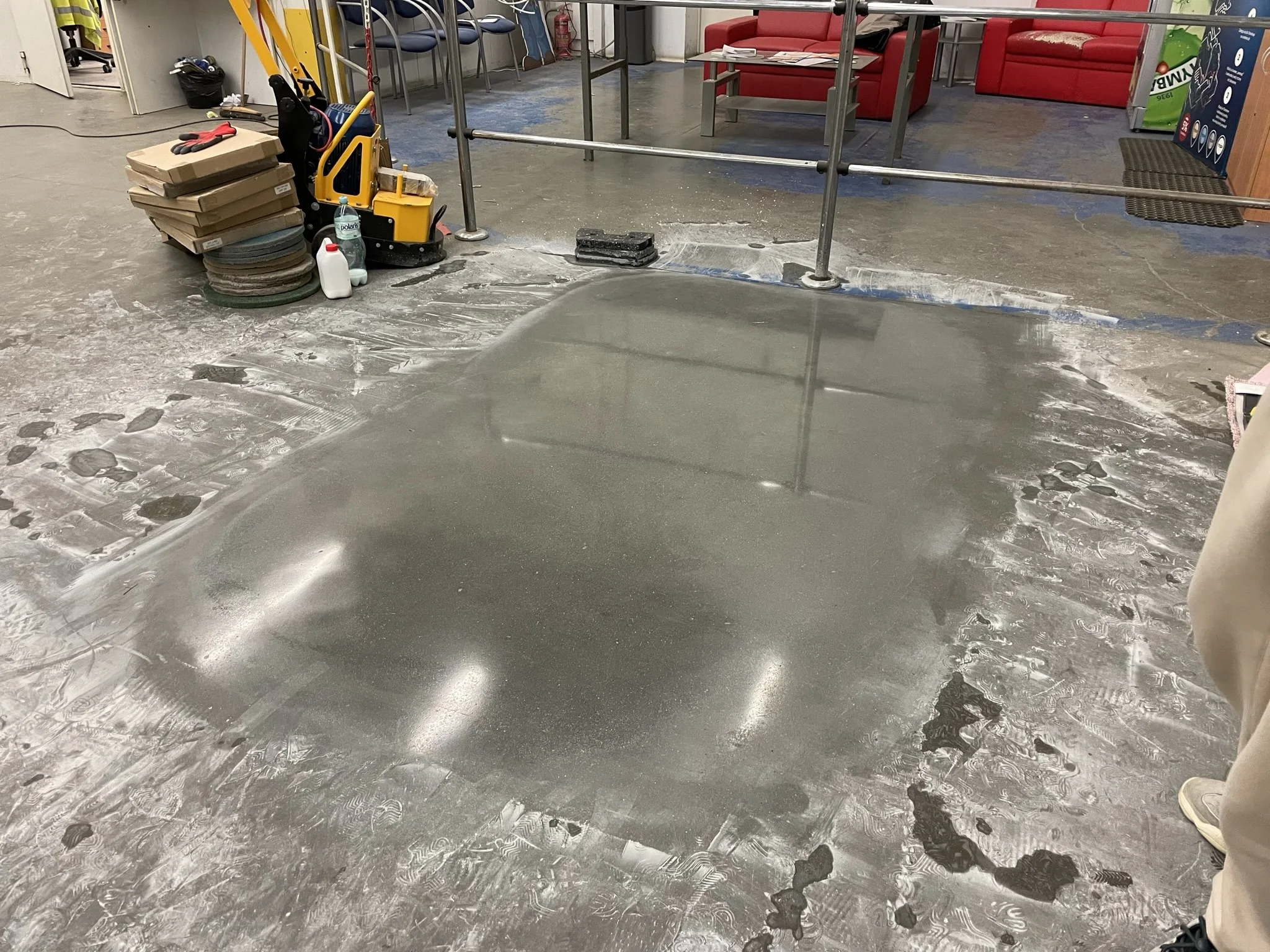
Compared to other types of industrial floors, polished concrete floors are also more economical. The cost of preparation and installation is often lower than other materials, and their long service life and minimal maintenance requirements result in savings over the years.
Even though concrete floor is used mainly for its functional properties, its aesthetics cannot be forgotten. Smooth, shiny floors add a professional look to the space and can also be individually designed in terms of colors and patterns to match the style of the interior.
Concrete floors are naturally resistant to many types of chemicals, making them an ideal choice for manufacturing companies and warehouses that may use a variety of chemicals during their operations.
Polished concrete floor is a solution that meets the expectations of the most demanding customers. Excellent functional properties, aesthetics, easy maintenance and favorable price are the reasons why this type of flooring has become so popular among warehouse and production owners.
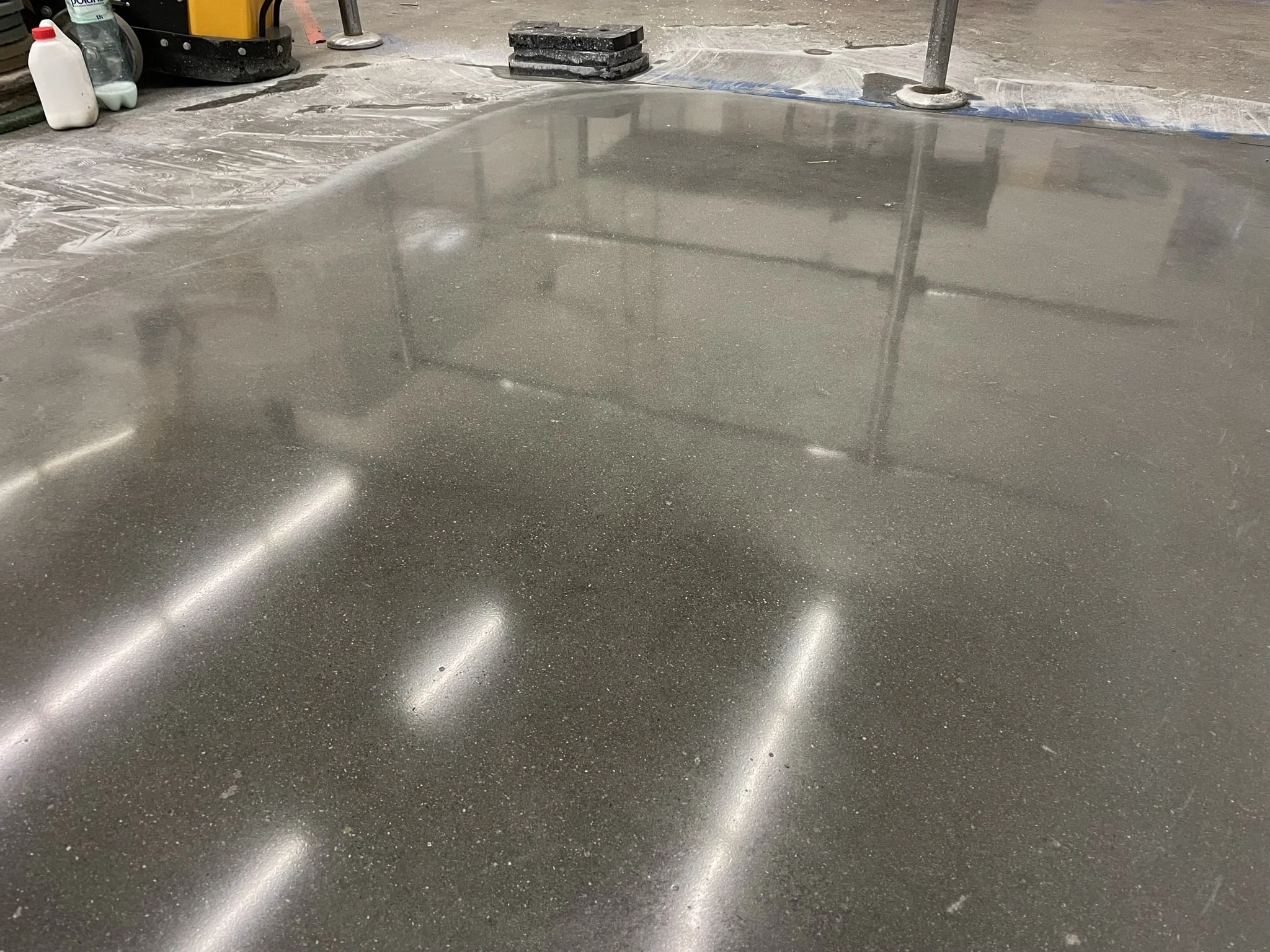
How to make a polished concrete floor from a regular concrete floor?
Modern architecture increasingly appreciates the natural beauty of concrete.
Especially concrete floors, which after polishing do not differ much in appearance from marble or granite finishes, and at the same time become much more resistant to damage. But how to make a polished concrete floor from a regular concrete floor? Here are some steps that may help you understand this process.
Before polishing begins, the concrete floor must be prepared. If it is contaminated, for example by oil contamination, it must be cleaned first. All unevennesses are also removed, industrial floors are repaired, cracks are filled and defects are reconstructed.
Polishing is carried out using specialized machines - the so-called polisher. This process is called grinding and involves the use of diamond discs of various gradations, which allows you to gradually smooth the surface until the desired texture and shine is achieved.
After polishing, it is necessary to seal the surface. Thanks to this, the floor gains an additional layer of protection against mechanical and chemical damage. This process is also known as impregnation. The final stage is wet polishing, which is the final mark on the procedure and gives the floor its final shine.
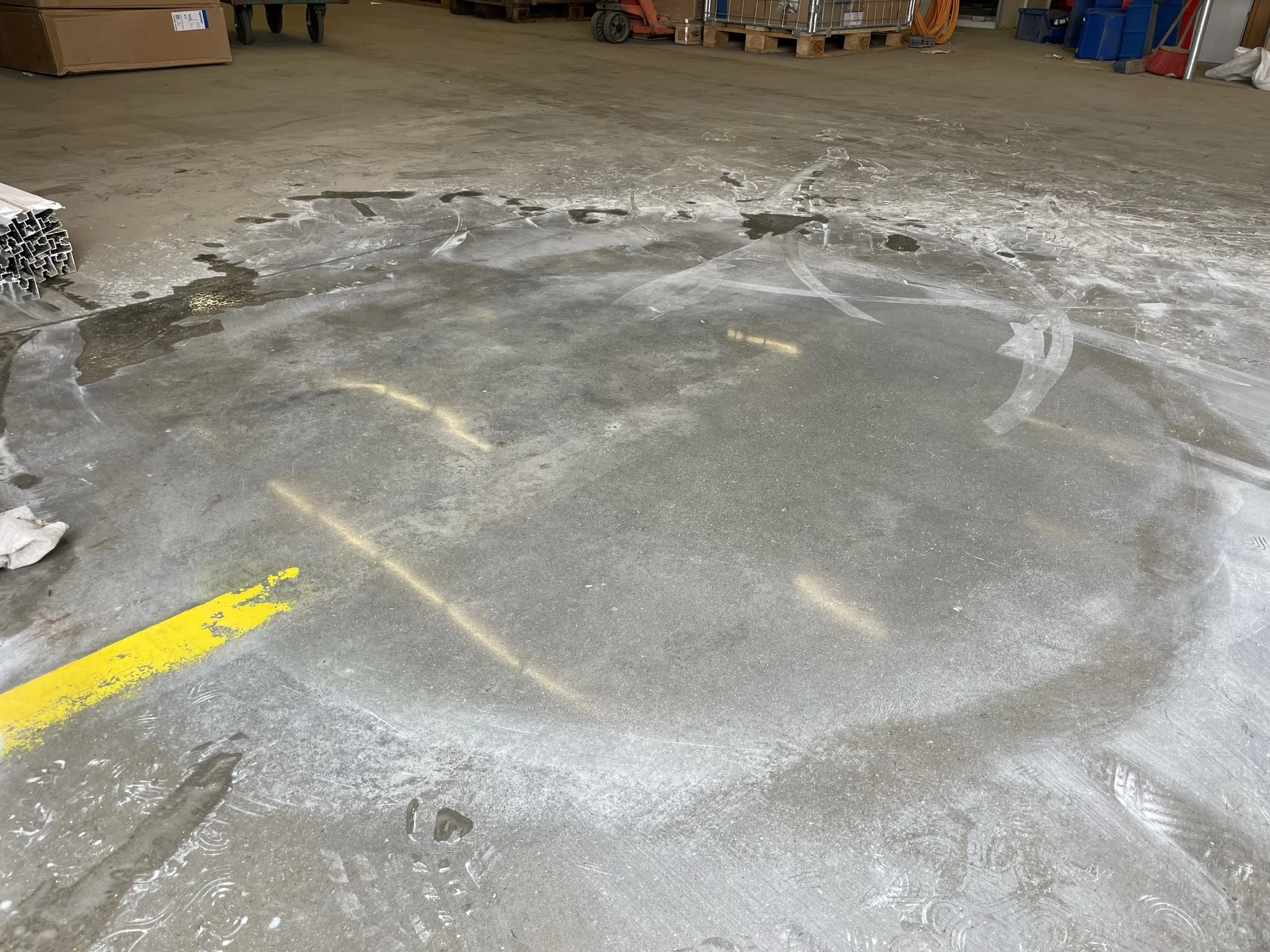
Of course, the precise implementation of these steps requires experience and specialized knowledge, which is why polishing the concrete floor should be done by professionals. A good quality polished concrete floor, done correctly, is a guarantee of strength and durability for many years.
It is worth emphasizing, however, that although a polished concrete floor is extremely durable and resistant to various types of damage, it requires regular care, which will ensure its aesthetic appearance for many years. Regular cleaning and maintenance should be the basis for keeping polished concrete floors in good condition.
The scope of work and costs associated with converting a plain concrete floor to a polished concrete floor can vary depending on many factors, including the initial condition of the floor, final appearance requirements, room size and other factors. Therefore, it is always worth consulting a professional to get an accurate quote and estimate of the scope of work.