Floor repair with resin. What Types of Resin Are There for Floor Repair?
Modern construction technologies offer a wide range of innovative solutions that enable effective and aesthetic floor repairs.
One of the most popular materials for floor repairs in this field are synthetic resins, which, thanks to their unique properties, such as high mechanical and chemical resistance, as well as ease of application, are gaining increasing recognition in both the industrial, commercial and domestic sectors. This article will introduce the different types of resins used for floor repairs and their most important features.
Epoxy resins are one of the most frequently chosen materials for repairing and finishing industrial floors. Thanks to their great mechanical strength and resistance to chemicals, they work perfectly in difficult operating conditions, such as warehouses, production halls or workshops. Epoxy resins also have excellent adhesion properties, which allows for effective repair of cracks and cavities in concrete.
Polyurethane is a material that stands out for its flexibility and resistance to abrasion. Polyurethane resins are therefore ideal for industrial floors, which are exposed to intensive use and multiple temperature fluctuations. In addition, they are resistant to UV radiation, making them a suitable choice for outdoor surfaces. Their aesthetic finish also makes them popular in sports and commercial facilities.
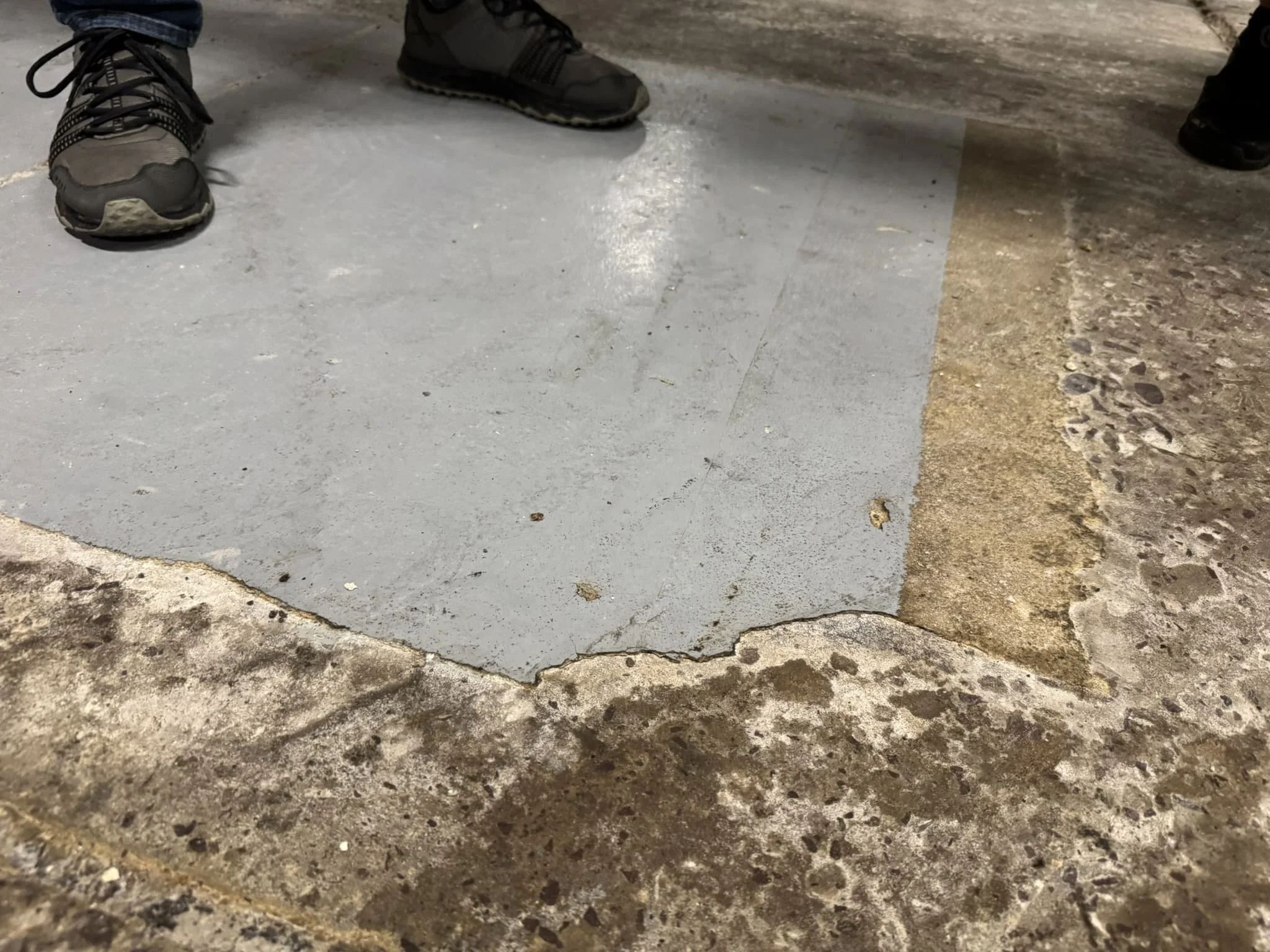
Methacrylic resins are characterized by a very fast curing time, which makes them invaluable in situations requiring immediate floor repairs. They are resistant to UV radiation, which prevents color fading and aesthetic changes to the surface. Because they can be applied at low temperatures, they are an ideal solution for use in various climatic conditions.
In addition to the above-mentioned properties, resins offer a number of other advantages that make them popular when installed on industrial concrete floors. Resins create highly resistant surfaces that not only protect against damage, but also extend the life of the entire floor. Availability in a variety of colors and finishes allows you to create a surface that is not only protective, but also decorative. Compared to traditional methods, such as concreting, resin repair is usually less time-consuming and requires shorter technological breaks.
Choosing the right type of resin for floor repair depends on the specifics of the location and its purpose. Regardless of the needs, synthetic resins offer flexibility, durability and aesthetics that make them an irreplaceable solution in modern construction. They enable both quick repair of minor damage and comprehensive renovation of large surfaces, while maintaining the highest standards of quality and aesthetics.
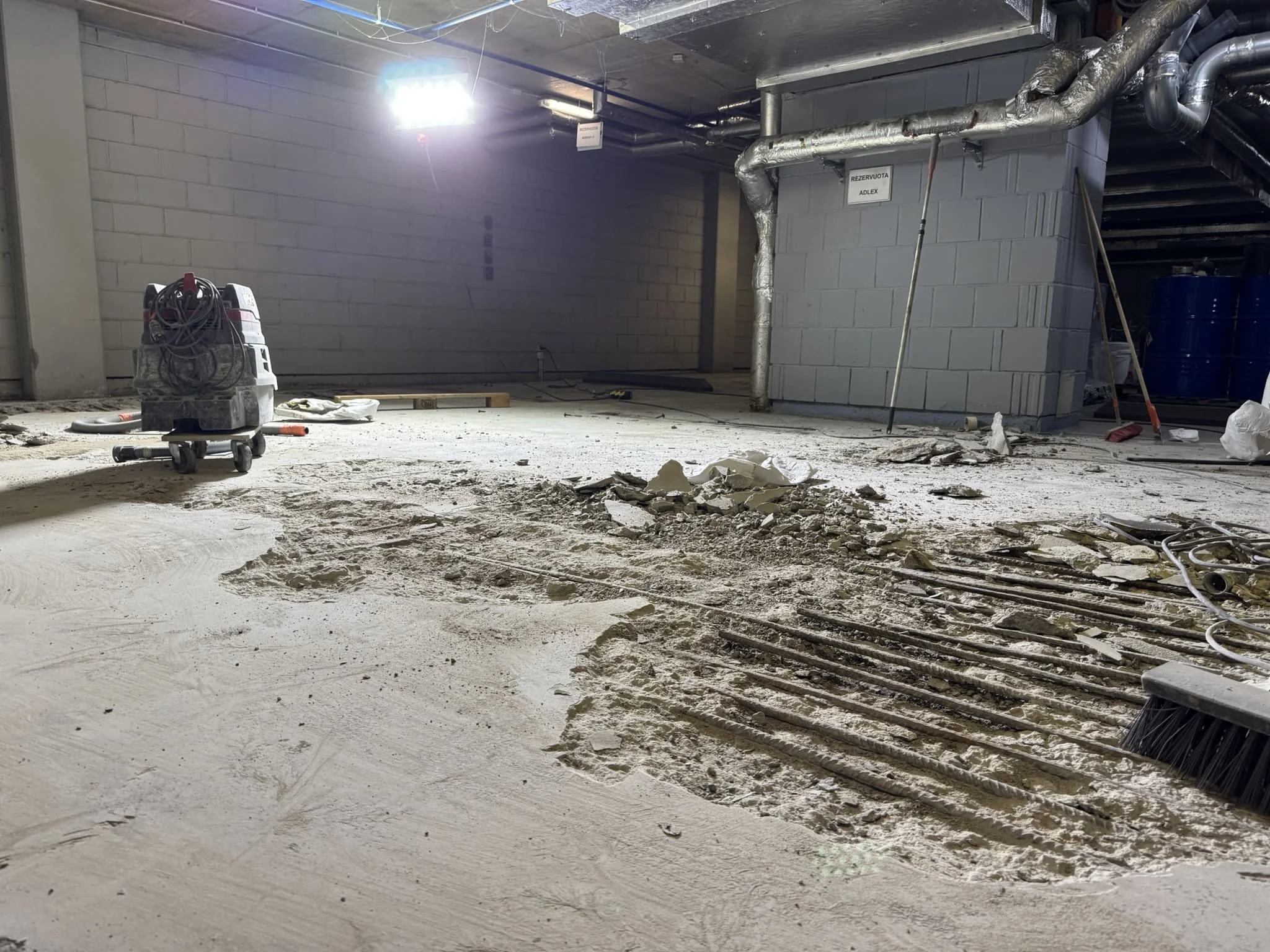
What are the main differences in floor repair using resin and cement?
Floor repair is an important element of maintaining its functionality and aesthetics.
Choosing the right repair method depends on many factors, including the specific nature of the damage, durability expectations, and budget. Two popular methods are resin and cement floor repair. Although both techniques aim to restore polished concrete to its original condition, they differ in several ways. This article will discuss the main differences between the two approaches.
Resins such as epoxy or polyurethane are very flexible, making them resistant to cracking due to substrate movement or temperature changes. Resin flooring this allows them to be used in areas exposed to high dynamic loads and in a variety of climatic conditions. Cement, on the other hand, is a less flexible material. In situations where the substrate is subject to high movement or extreme temperature fluctuations, cement can crack, leading to the need for more frequent repairs.
One of the significant differences between floor repair with resin and cement is the time it takes to cure and achieve full functionality of the floor. Resins, especially methacrylate resins, have a fast cure time – often just a few hours, which minimizes downtime and allows for a quick return to service. In the case of cement, the drying and curing time is much longer, usually several days, which can be critical in industrial environments where time is money.
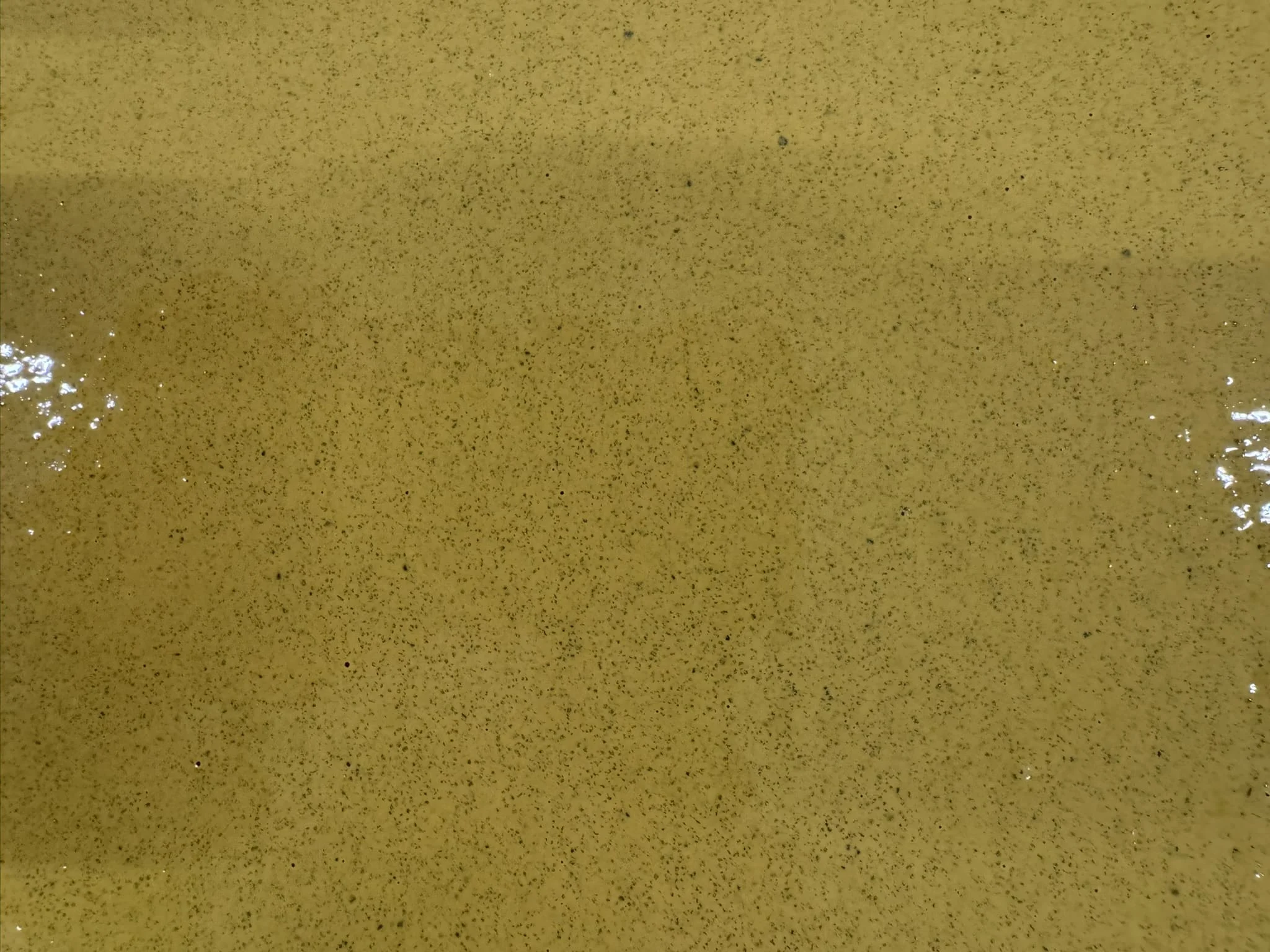
Resins offer higher resistance to chemicals than cement. That is why they are often used in places where repaired floor is exposed to contact with chemicals, such as laboratories, industrial plants or chemical warehouses. Cement does not have such resistance and can be degraded by aggressive chemicals, which requires additional protective measures.
Resins offer a wide range of aesthetic finishes, including the ability to choose colors, gloss, and decorative effects such as marble imitations. This makes them a popular choice in areas where appearance is important, such as offices and commercial properties. Cementitious finishes floor repairs are more austere and limited in aesthetics. Although cementitious floors can also be stained or coated with protective layers to enhance their appearance, they usually do not match the aesthetics offered by resins.
The costs associated with using resins for floor repair can be higher compared to cement, especially when using specialist high-performance resins. However, the benefits in durability, speed of application and aesthetics often make up for the higher initial expense. Cement is usually a more economical material option, but the costs associated with a longer lead time and the potential need for more frequent repairs can impact the overall budget.
The decision on the method of floor repair should be made based on a thorough analysis of the needs and operating conditions. Resins offer flexibility, fast curing time, high chemical resistance and wide aesthetic possibilities, while cement is a more traditional and often cheaper solution. Each approach has its advantages and disadvantages, which should be considered when planning renovation work.