What types of industrial flooring are there in the world?
Modern industries require solid, durable and functional flooring solutions.
Choosing the right type of industrial flooring is crucial to the safety, efficiency, and aesthetics of your workspace. There are several types of industrial flooring that vary in their properties and applications. Let’s take a look at the most popular ones.
Concrete floors are among the most commonly used in industry due to their durability and resistance to abrasion. Commonly used in warehouses, production halls and logistics centers, concrete floors provide longevity and ease of maintenance. Industrial floor can be reinforced with additives such as steel or glass fibers, which further increases its durability.
Resin floors, also known as epoxy floors, are characterized by high chemical and mechanical resistance. They are used in places where the floor is exposed to aggressive chemicals, such as laboratories, chemical plants or the food industry. Thanks to their smooth surface, they are easy to keep clean, which is crucial in places with high hygiene standards.
Polyurethane industrial floors are characterized by high flexibility and impact resistance, which makes them ideal for places where the substrate is exposed to dynamic loads. They are used, for example, in sports halls and multi-storey car parks. Additionally, polyurethane floors are resistant to UV radiation, so they do not fade under the influence of sunlight.
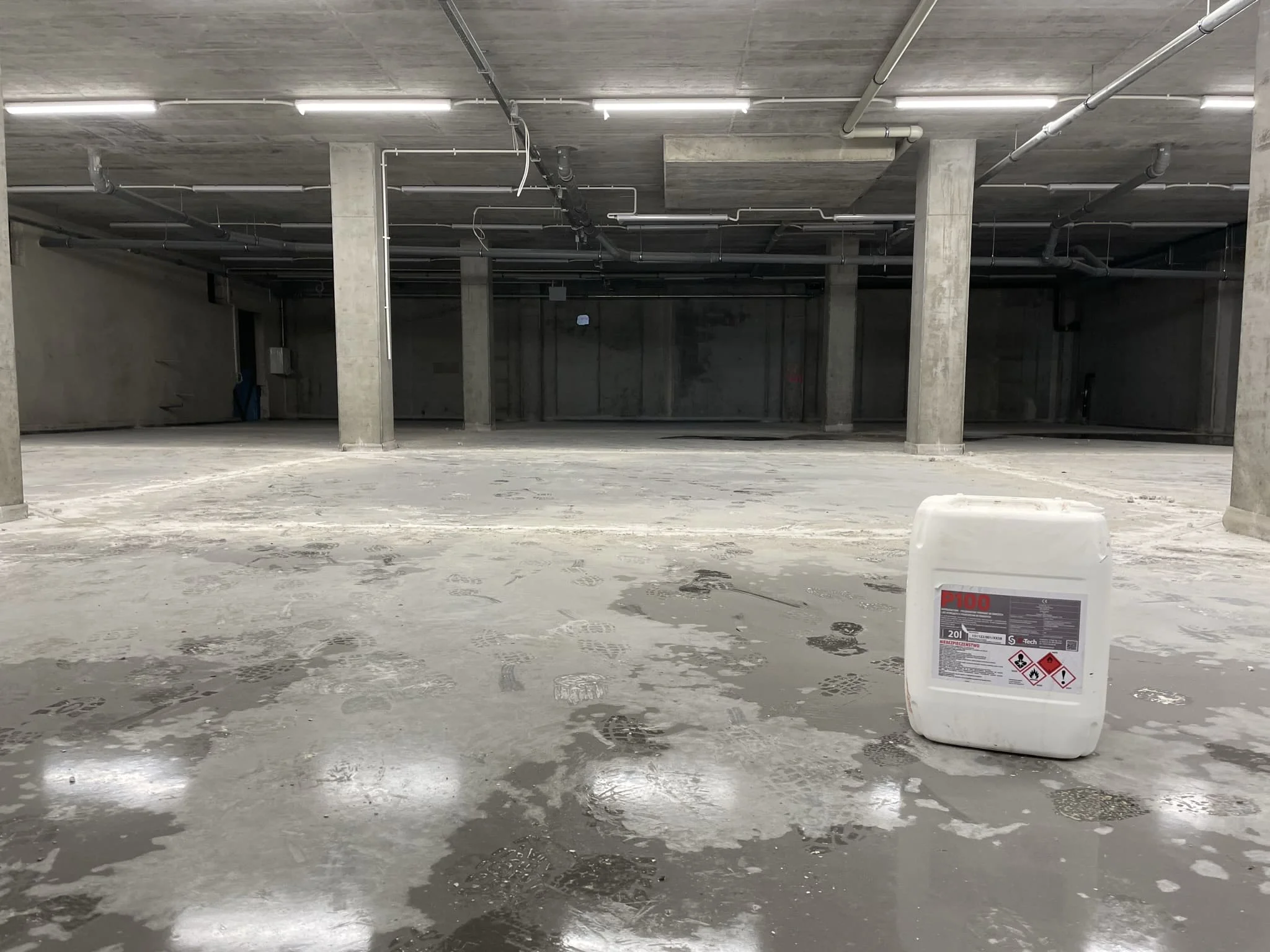
Industrial floors antistatic are specialist solutions used mainly in the electronics, pharmaceutical and pyrotechnic industries. Their task is to discharge electrostatic charges, which minimizes the risk of damage to sensitive electronic devices and prevents the formation of sparks that could lead to explosions.
Acid-resistant floors, as the name suggests, are designed to withstand the effects of acids and other aggressive chemicals. They are used in the chemical and pharmaceutical industries, where there is no room for any damage caused by corrosive substances.
Ceramic floors, although less commonly used in heavy industry, are used in places with high sanitary requirements, such as industrial floors in kitchens or food processing plants. They are characterized by resistance to high temperatures and ease of cleaning.
Rubber floors are flexible and non-slip, making them ideal for workplaces where employee safety is a priority. They are often found in the automotive sector and in areas where there is a high risk of falls, such as assembly stations.
Each type of industrial floor has its own unique properties and applications. Choosing the right one depends on the specific requirements of a given work environment – from mechanical and chemical resistance to hygiene and aesthetic requirements. When investing in industrial space, it is worth consulting with specialists to choose the solution that best meets the needs of a given plant.
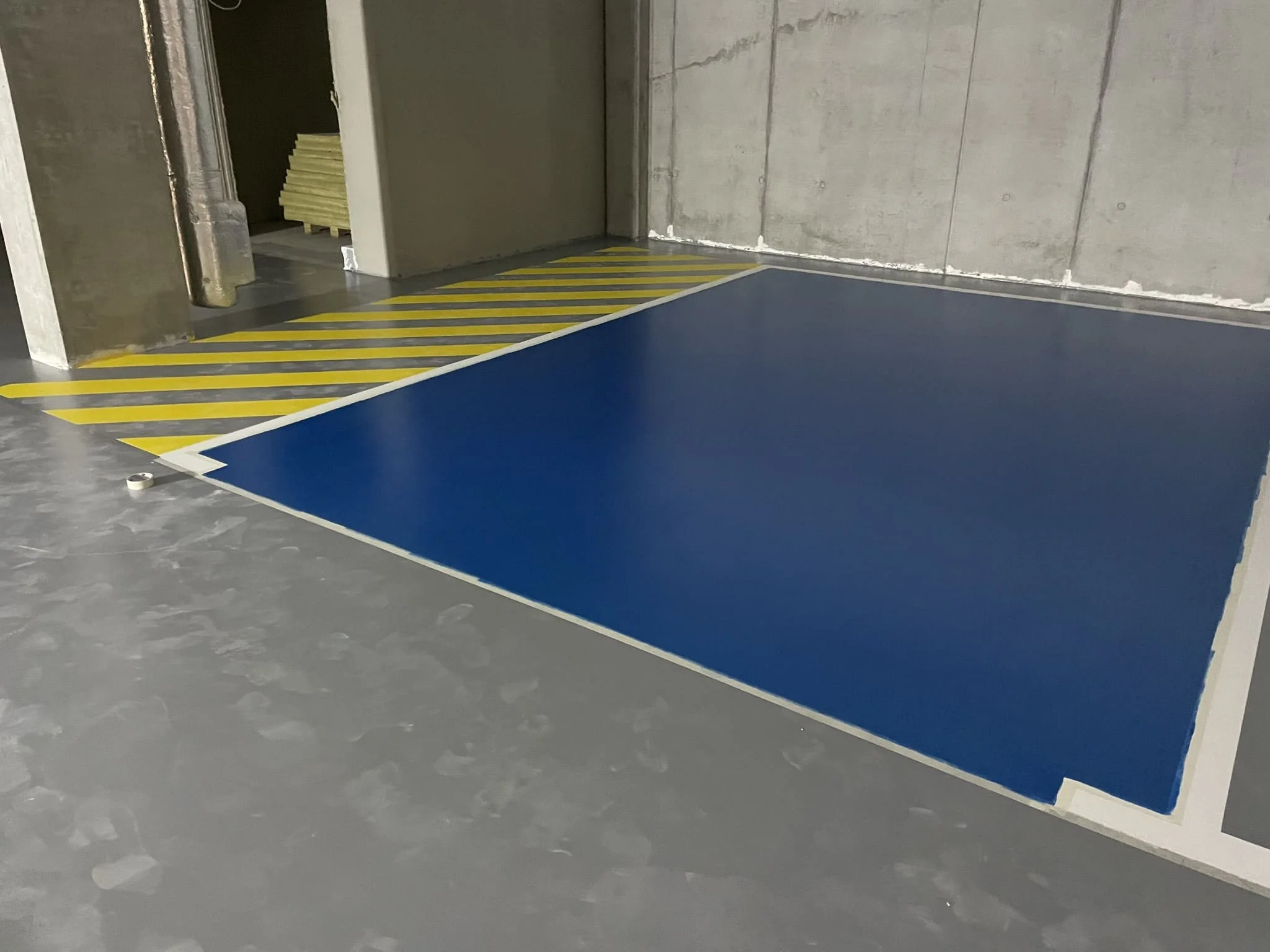
What are the differences between industrial concrete and resin floors?
Selecting the right industrial flooring is a key element in planning and managing workspaces.
The two most popular options are concrete and resin floors. While both offer a number of benefits, they differ in many ways, from strength and chemical resistance to cost and installation time. Below are the main differences between these two types of industrial flooring.
Concrete floors are made from a mixture of cement, aggregate (grit) and water. During setting, concrete creates a solid, uniform structure. Concrete floors can be additionally reinforced with steel or glass fibers to increase their resistance to mechanical loads. During pumping concrete it is necessary to maintain the desired consistency of the concrete.
Resin floors are made of a mixture of synthetic resins, most often epoxy or polyurethane, with various additives. These resins can be applied in several layers, which allows for obtaining different mechanical and chemical properties of the surface.
Industrial floors made of concrete are highly resistant to mechanical loads, making them ideal for places with heavy equipment traffic, such as warehouses or production halls. They are also abrasion resistant.
Although resin floors are also characterized by high durability, their greatest advantage is resistance to various chemicals. Epoxy resins are resistant to acids, alkalis, solvents and other chemicals. Polyurethane resins are also characterized by flexibility, which makes them resistant to dynamic loads and impacts.
Concrete floors are typically cheaper to install, making them an attractive option for large areas. However, costs can increase if additional reinforcement or special finishes, such as polished concrete, are required.
Resin floors are usually more expensive compared to industrial concrete floors, due to the higher cost of materials and the more complicated application process. However, their durability and special chemical properties may justify the higher cost, especially in high-demand environments.
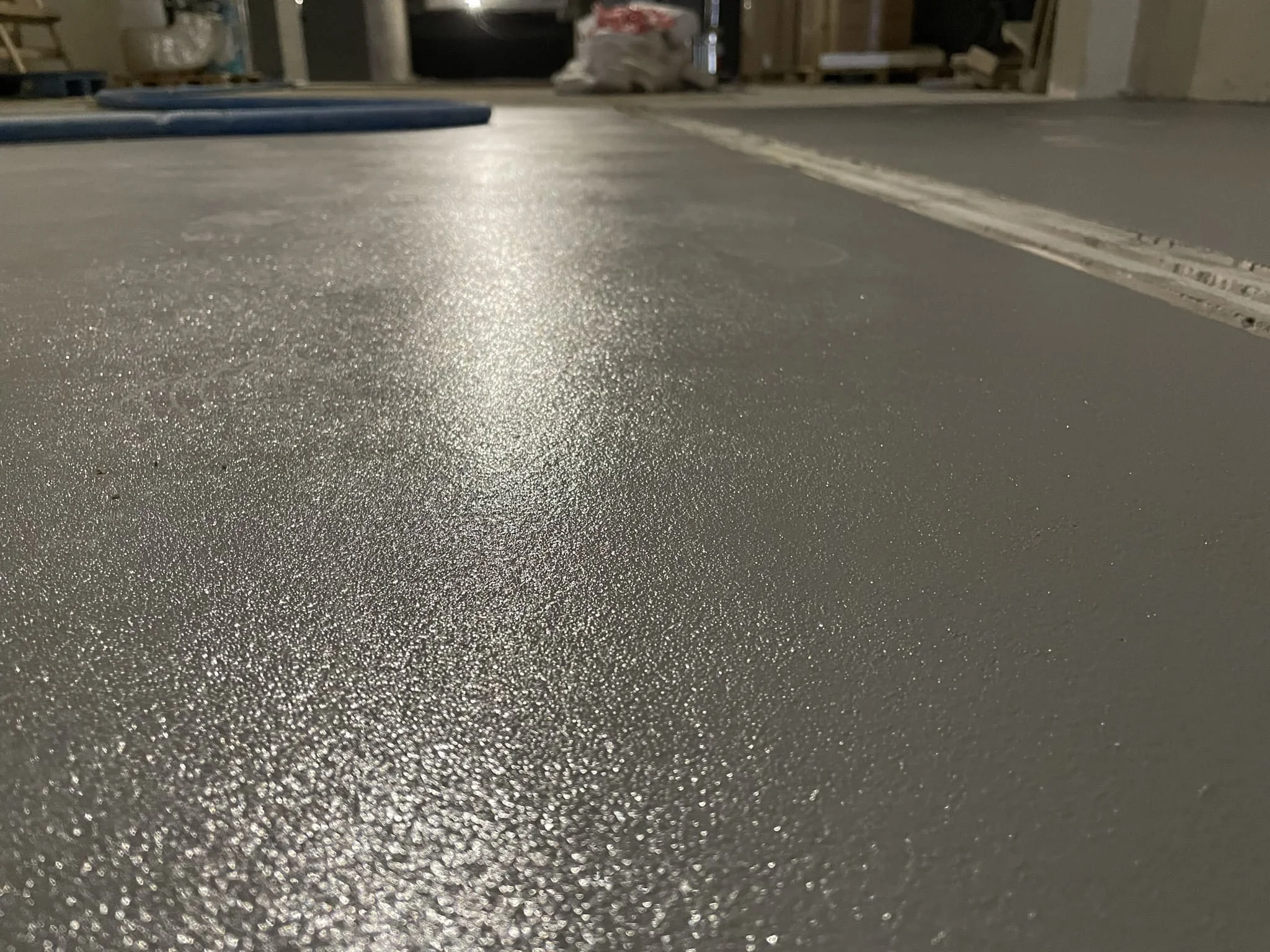
Installing concrete floors is a time-consuming process. The concrete must be properly mixed, spread and leveled, and then it needs time to cure. The cure time can take anywhere from a few days to a few weeks, depending on the conditions. If standard industrial concrete is not an option, thin-layer commercial cement floors come to the rescue.
Resin floors, compared to industrial concrete floors, have a much shorter installation time. Once the resin is applied, it only takes a short time for it to cure (usually from a few hours to a few days, depending on the type of resin and conditions).
Industrial concrete floors provide a raw, industrial aesthetic that can be attractive in some contexts. However, they can also be modified by polishing, staining, or applying different surface finishes.
Resin floors offer greater personalization options. They can be dyed in almost any color, and can also be enhanced with various effects, such as metallic reflections or additional decorative layers of industrial floors. This makes them a popular choice in more aesthetically demanding spaces, such as laboratories, office spaces or retail facilities.
Concrete floors are relatively easy to maintain, but may require periodic sealing to prevent floor repairs to prevent stains and chemicals from absorbing. Cleaning can be more labor-intensive, especially if the surface has not been properly sealed.
Resin floors are easy to keep clean thanks to their smooth, seamless surface that does not absorb liquids and is resistant to stains. They require minimal maintenance – regular cleaning is usually enough to maintain their aesthetics and functionality. And the use of safety barriers helps maintain safety in the production or storage area.
The choice between concrete and resin flooring depends mainly on the specific needs and requirements of the working environment. Industrial concrete flooring is ideal for heavy mechanical applications, offering high durability at a lower installed cost. On the other hand, resin flooring, although more expensive, offers excellent chemical resistance and greater customization options, making it an ideal solution for more demanding and diverse applications. The final decision should be made after careful consideration of all factors, including cost, installation times and specific operational requirements.