Concrete floor repair methods. Causes of concrete damage. Types of concrete floor damage.
Concrete floor repair in car parks is key to durability and safety. Car parks, especially in public buildings, are places with specific requirements in terms of surface durability.
Concrete floors in both underground and surface parking lots are exposed to a number of adverse factors, including heavy traffic, moisture, chemicals from vehicles, and changing weather conditions. As a result, regular inspection and repair of the concrete surface are essential to ensure its durability and user safety. In this article, we will look at the main causes of concrete floor damage, methods of repair, and best maintenance practices.
Understanding why concrete, a material that is generally considered durable, deteriorates is essential to effective floor repair and maintenance. Here are some of the reasons why concrete can deteriorate in parking lots. Parking lot floors must withstand significant traffic, especially heavy vehicles. This constant mechanical loading can lead to the formation of micro-cracks that can expand over time, causing more structural damage.
In unroofed areas, sudden temperature changes, freezing and thawing, and exposure to UV radiation can lead to cracking and erosion of the concrete industrial floor surface. Chemicals from vehicle fluids and winter de-icing agents can contribute to the chemical degradation of concrete. Water penetrating the concrete can lead to corrosion of the reinforcement and weaken the structure through freeze-thaw cycles.
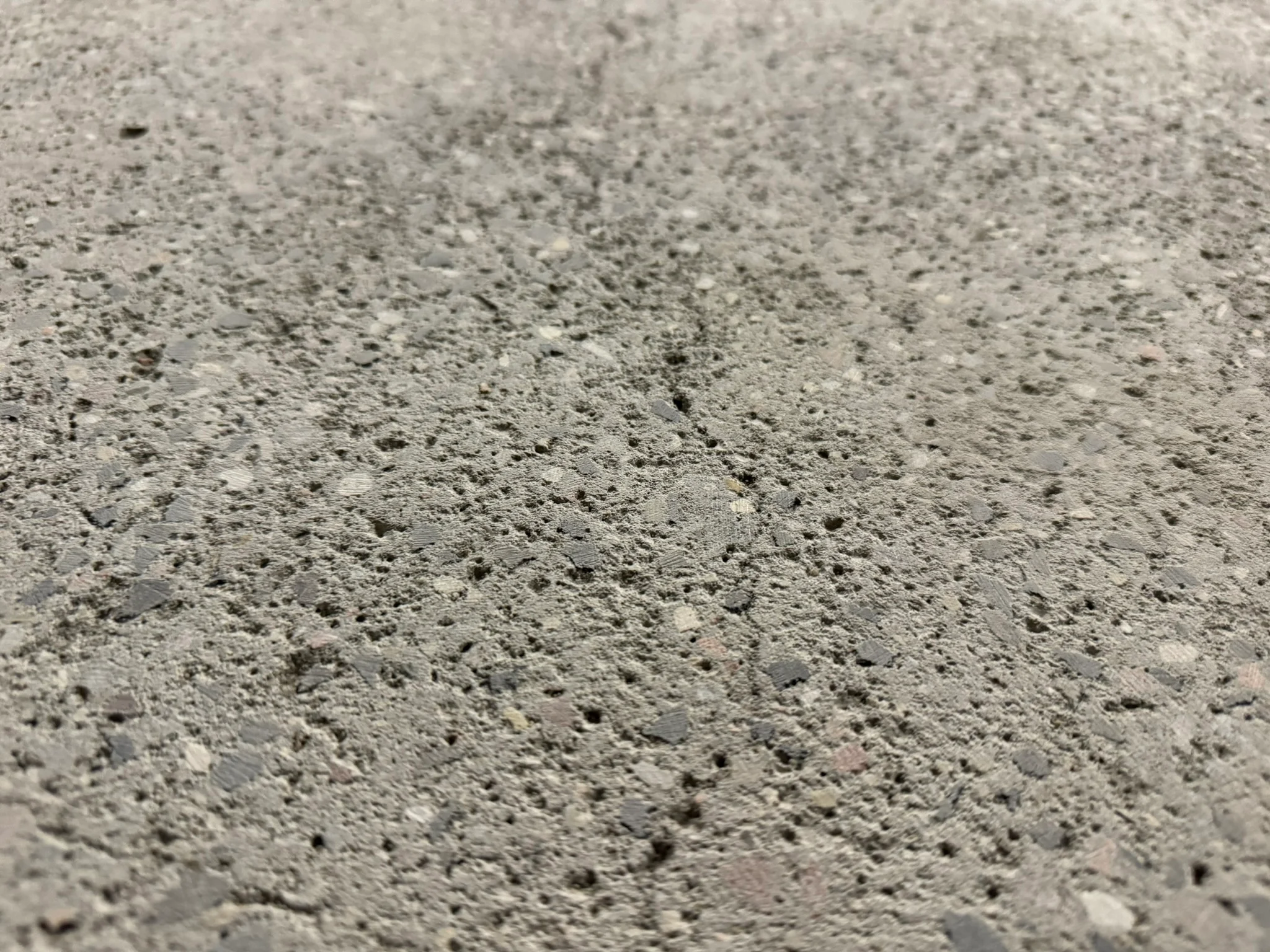
Parking thin-layer commercial cement floors may be subject to various types of damage, including. They may be the result of problems with the substrate, inadequate quality of the concrete mix or lack of or improper execution of expansion joints. They may result from insufficient preparation of the substrate or conditions related to errors in the process of mixing and applying the concrete.
Most often they are caused by point loads, but can also be the result of local chemical damage. It occurs due to the penetration of water and aggressive chemicals into the concrete, which leads to a loss of structural integrity and the need for concrete parking lot floor repair.
Depending on the type and extent of damage, different concrete floor repair techniques are used. Crack repair most often involves injecting specialist resins (e.g. epoxy or polyurethane) into the cracks, creating permanent fillers that effectively prevent further crack development and provide a smooth surface.
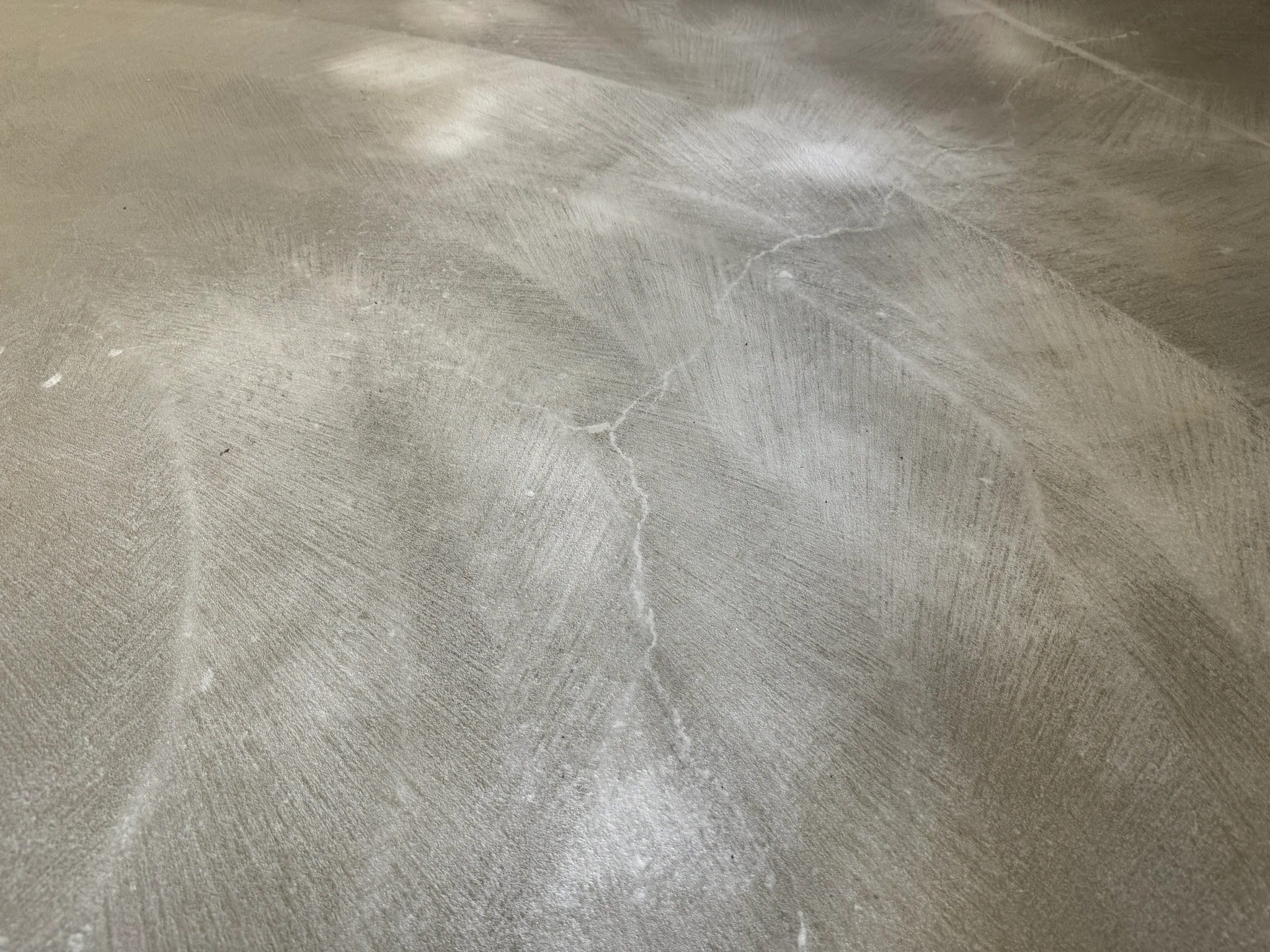
Renovation of parking lot floor surface.
In case of surface problems, mechanical methods are most often used, such as concrete milling, which is accompanied by the removal of damaged layers.
Then a repair layer is applied, such as polished concrete, which may be enriched with additives that improve the abrasion and weather resistance parameter.
Deep defects are usually repaired using resin floors that are properly prepared in terms of adhesion and mechanical properties. In the case of large defects, reinforcement with steel rods or composite mats is used to ensure the stability and durability of the repair.
After parking lot floor repair, especially after new surface coatings, it is crucial to apply appropriate waterproofing and chemical protection coatings. Thanks to them, the concrete surface is protected against the ingress of water and aggressive chemicals.
While concrete floor repair is an important part of maintaining your surface, regular maintenance plays a key role in preventing the need for frequent and costly repairs. Here are some tips for maintaining concrete floors.
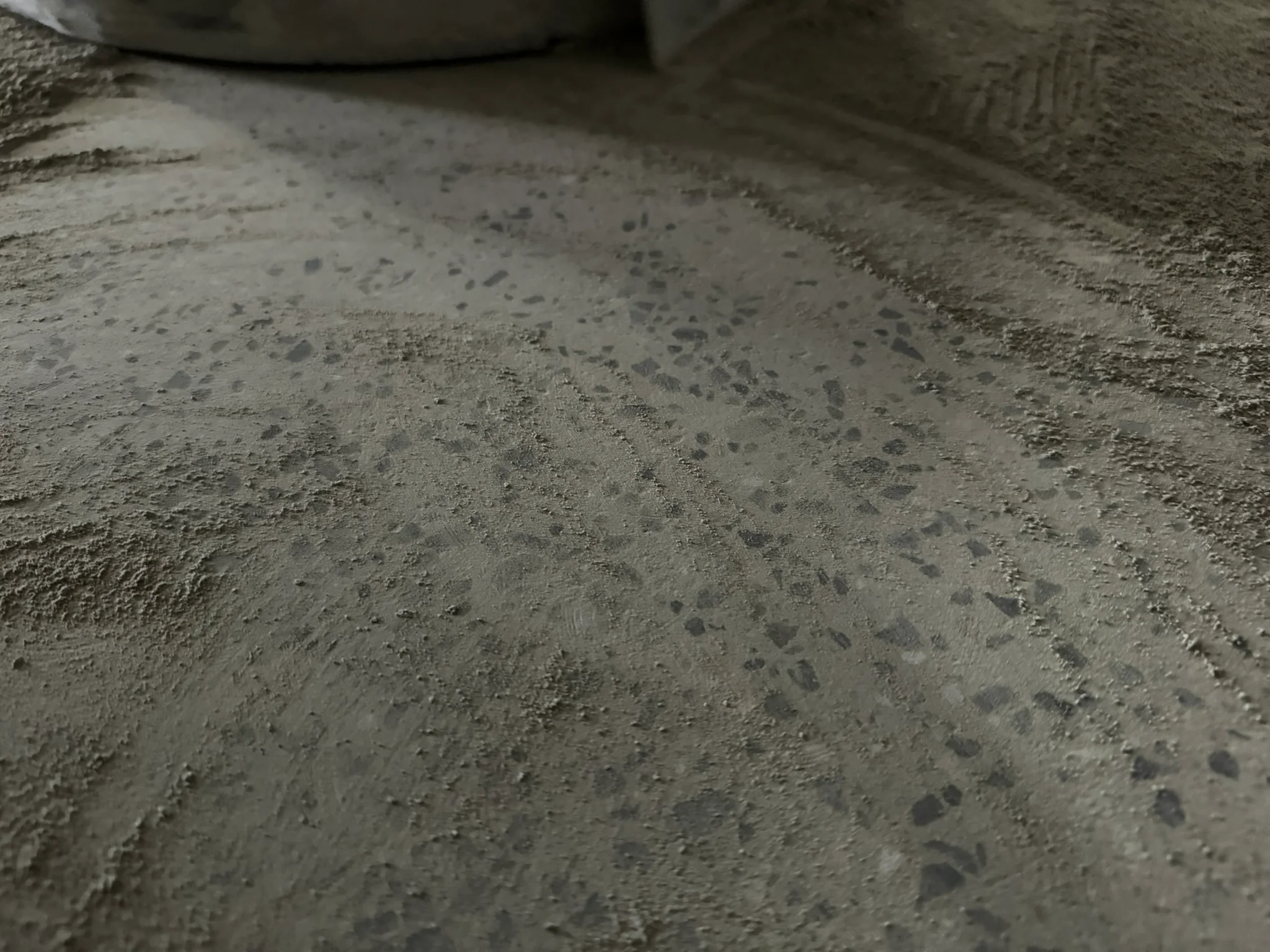
Regular inspections of the condition of the repaired parking lot floor allow for early detection of problems and rapid additional repair actions. Cleaning the surface of dirt such as oils, grease and abrasion particles minimizes their harmful effect on the concrete.
Regular application of impregnation coatings in industrial floors and weather-resistant floors extends the life of the surface. Ensuring that actual loads match the design assumptions provides additional protection against potential damage. An effective drainage system prevents puddles, which reduces the risk of water penetration.
Repair and maintenance of concrete floors in parking lots is a process that requires specialist knowledge and the use of appropriate technologies. Properly performed repairs and regular maintenance not only extend the life of the surface, but also ensure the safety of parking users. By understanding the specifics of damage and choosing the right methods for their repair, concrete floors can serve for many years, providing a reliable foundation for parking infrastructure. The introduction of systematic maintenance practices supports the durability of these surfaces, minimizing the need for further interventions and ensuring optimal conditions for everyday use.