How to pump concrete in difficult conditions when a regular pump cannot be used?
Concrete pumping is a key part of many construction projects, enabling material to be delivered quickly and efficiently to hard-to-reach areas.
However, what to do in situations where standard concrete pumps for industrial concrete floors prove ineffective or impossible to use? Here are some methods and techniques that can be used in extreme conditions.
Where traditional piston or rope pumps fail, pneumatic and screw pumps can be an alternative. Pneumatic pumps use compressed air to move concrete through coils, which is particularly effective in tight or high-altitude areas for polished concrete. Screw pumps, on the other hand, feature a screw helix that moves the concrete continuously and evenly, minimizing the risk of blockages.
In extreme situations, especially in hard-to-reach mountainous areas or at high altitudes, helicopters can be used to transport concrete instead of pumping concrete. The concrete is then transported in special containers or buckets suspended from the helicopter. Although this is a fairly expensive method, it works well in situations where there is no other option.
In difficult conditions, pipes and flanges with specific properties are sometimes used. For long distances, slopes and levels, special pipes with anti-adhesive internal coatings can prevent concrete from sticking to the pipe walls, reducing the risk of blockages. Reinforcing flanges added at key points in the pipeline system can prevent leaks.
Classic concrete pumping methods may not seem innovative, but in many situations they are irreplaceable. To deliver concrete to the site, construction teams can use small loaders that transport the material to where it is needed. In difficult terrain, four-wheel drive dump trucks can transport concrete for specific distances, from where it can then be spread manually.
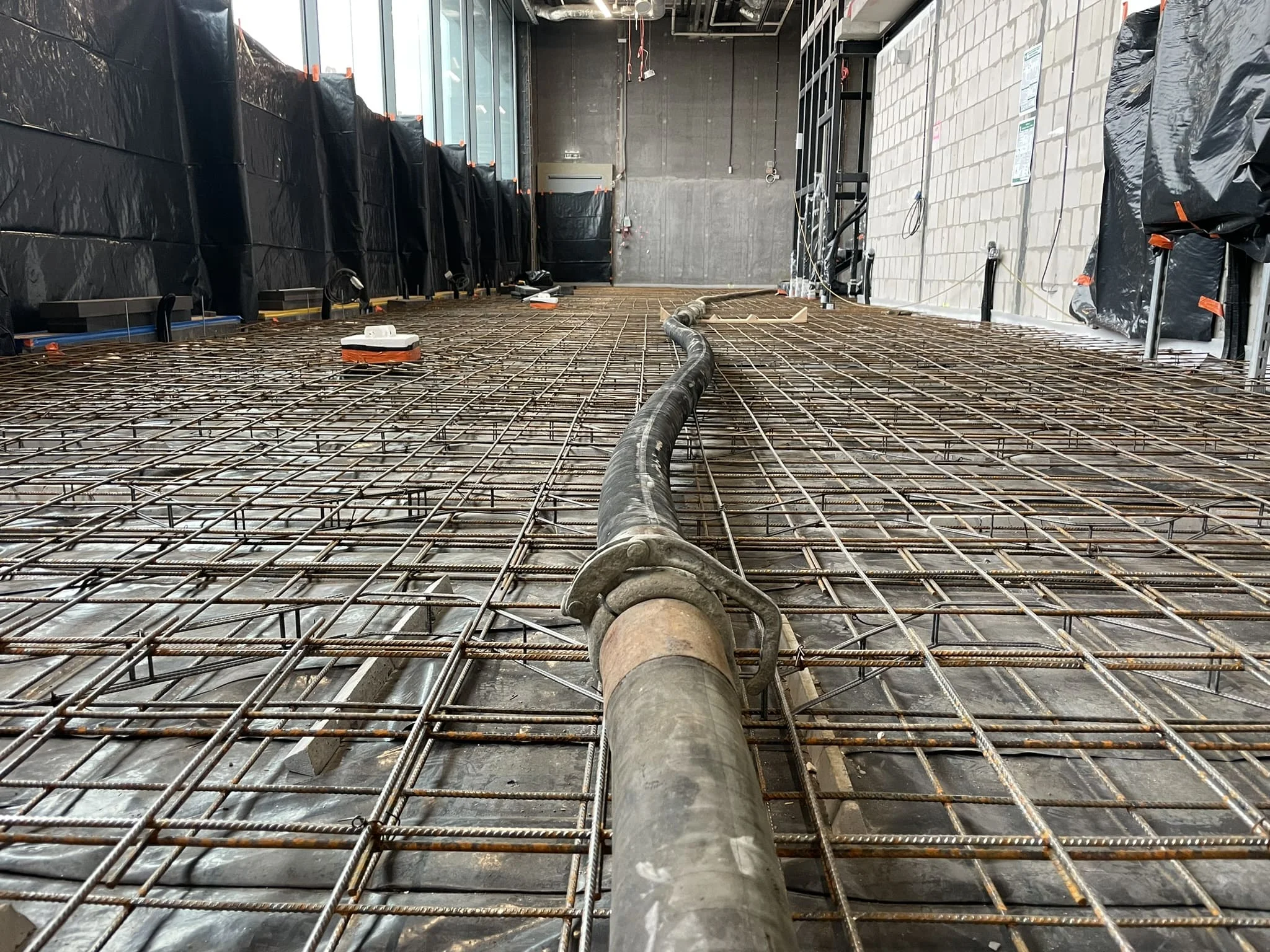
In the case of resin flooring, when concrete needs to be precisely distributed in hard-to-reach places, vibration technology can be invaluable. Advanced vibration devices help to liquefy concrete, allowing it to reach every nook and cranny of the structure without the need for high pressures or long pipe installations.
While this may seem primitive, in extreme conditions, hand pumps and pourers are worth considering. These simple devices allow for precise control of the flow and amount of concrete. With the right techniques, concrete can be applied efficiently and precisely to small areas.
An innovative solution is the hydroprogrammed concrete pumping systems. These advanced devices use computer technology and sensors that automatically adjust pressures and flows. This allows for precise control of the pumping process even in the most demanding conditions.
Pumping concrete in difficult conditions is a real challenge that requires innovative technical solutions. Depending on the specifics of the project, you can reach for a variety of technologies from simple hand pumps, through modern pneumatic and screw pumps, to advanced vibration and hydroprogrammed systems. Each of these solutions has its advantages and disadvantages, which is why careful planning and adaptation of methods to the specifics of the terrain conditions and technical requirements of the project play a key role here.
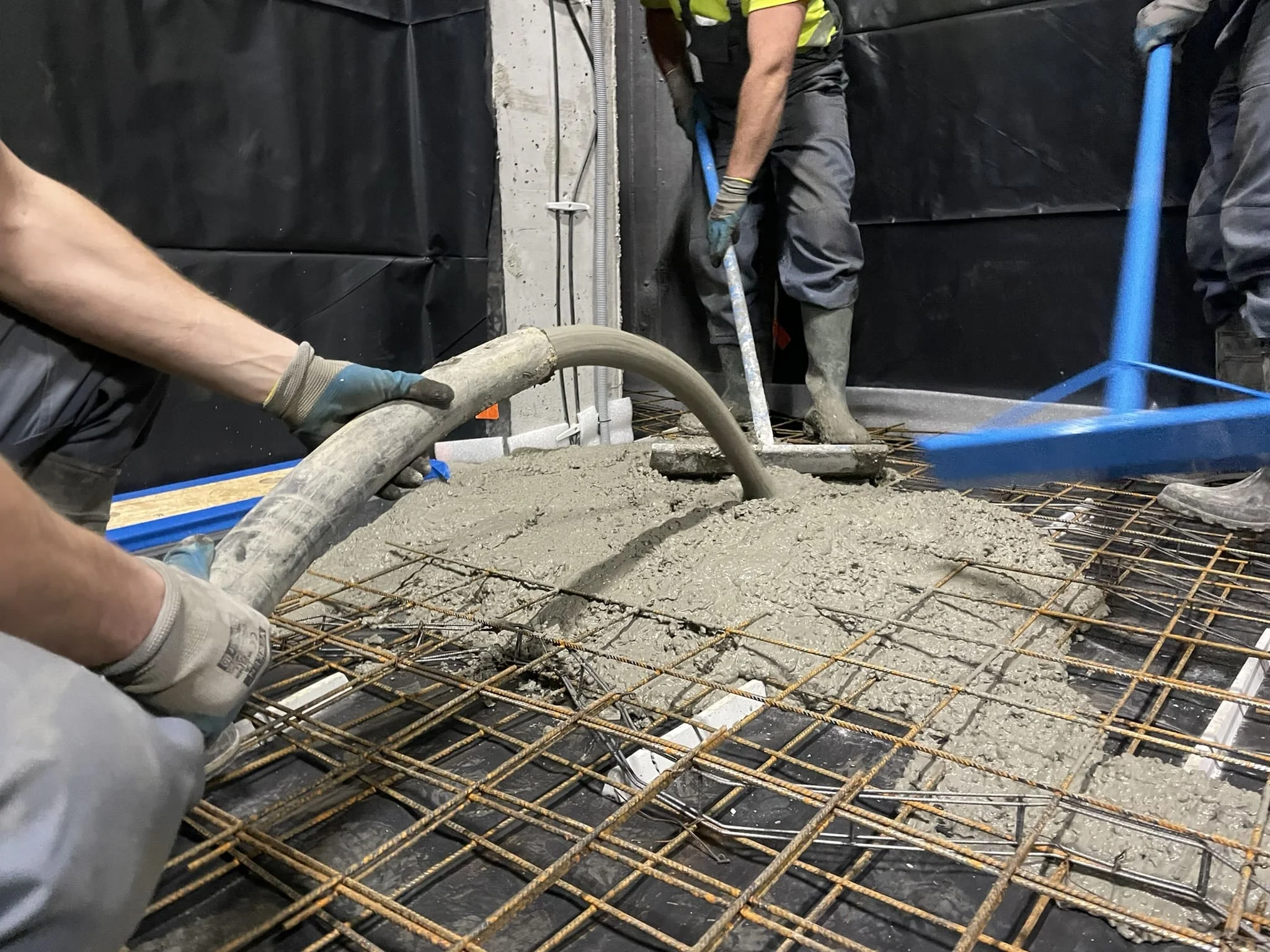
Pumping concrete into a single-family home
When planning to build a single-family home, one of the key construction stages is pouring the foundations, walls, and columns.
Pumping concrete is a reliable and efficient way to deliver this material to the construction site. In this article, we will show you how to properly pump concrete to ensure the durability and safety of the structure.
Concrete pumping allows for quick and precise delivery of material to locations and industrial floors that may be difficult to access with traditional transportation methods such as wheelbarrows or hand pouring. Concrete pumps can move concrete over long horizontal and vertical distances, which is particularly useful in single-family housing construction.
Pumping concrete ensures the homogeneity of the concrete mix, which is crucial for ensuring the proper strength of the structure. Continuous mixing during the transport of concrete by means of a pump prevents segregation of the concrete components.
Before starting to pump concrete, the construction site must be properly prepared, and floor repairs must be made. It is important that the ground is level and stable, and that all parts of the installation are properly attached.
Next, we install the pumping system. The pipes and hoses that will transport the concrete must be properly secured and sealed to avoid leaks and loss of material.
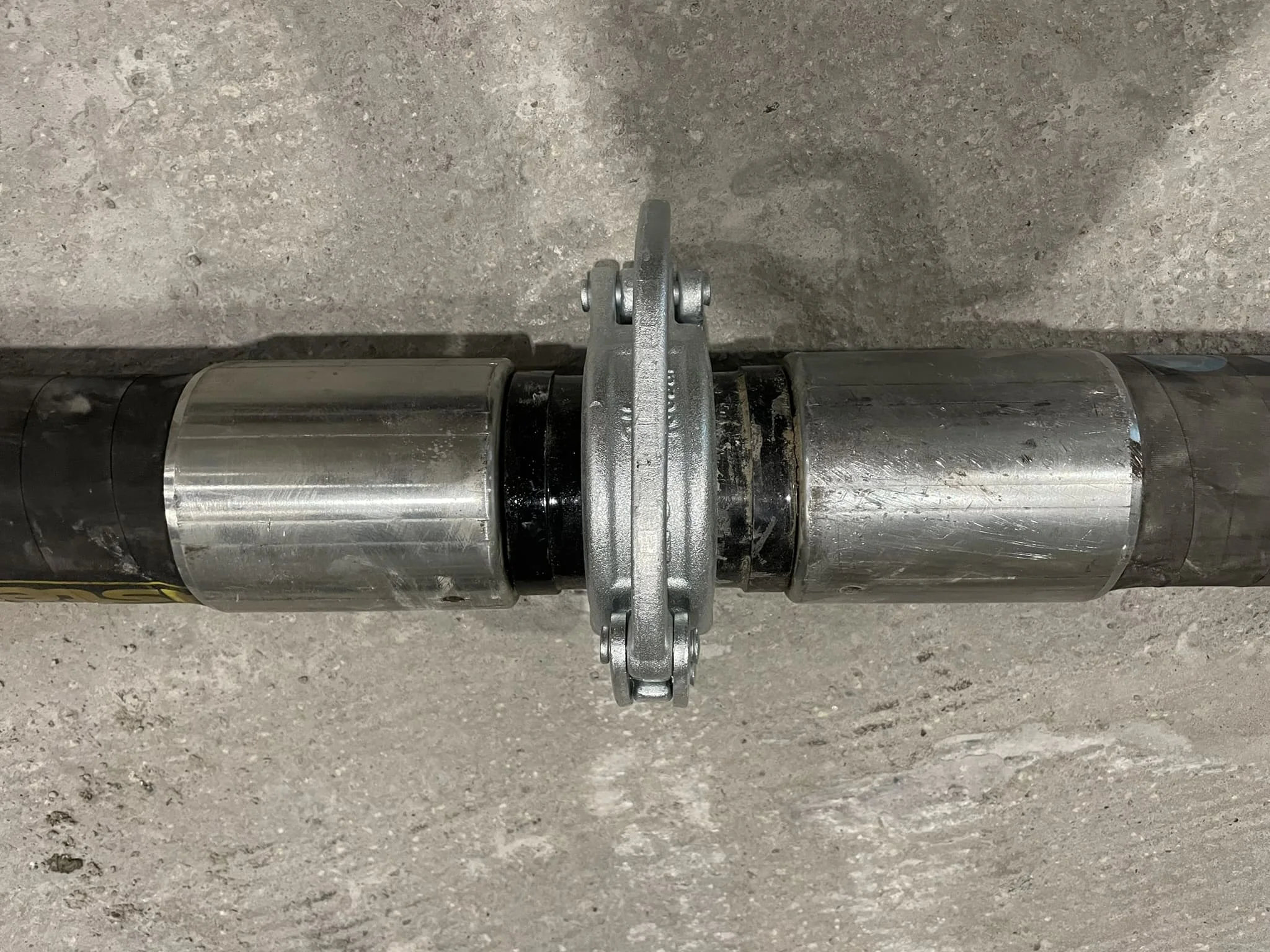
Before starting concrete pumping it is worth checking the quality of the concrete. It should properly meet the standards for the specification of the concrete mix, and the consistency of the concrete should be adapted to the type of pump used.
Once everything is ready, we can start pumping the concrete. This process should be monitored by experienced operators to ensure its smoothness and uniformity. In case of downtime, the concrete should be pumped regularly to prevent blockages.
Once the pumping is complete, the concrete must be properly finished and compacted using vibrators. This process removes air bubbles and ensures proper cohesion of the concrete mix.
Safety on the construction site is a priority. Make sure all equipment is in good working order and that workers are properly trained in the operation of concrete pumps. Personal protective equipment such as hard hats, safety glasses and gloves should also be worn. One of the main basics of safety is safety barriers.
Pumping concrete into a single-family home is an effective and precise way of delivering this material to the construction site. Using the right equipment, taking care of the quality and safety of work, we can ensure a durable and strong structure. Remember that a well-planned concrete pumping process is the key to the success of any construction.