What did we do on this construction site:
- construction of industrial concrete floor.
How to protect industrial concrete floors from freezing?
Industrial concrete floors are widely used due to their strength and durability.
However, during the colder months, especially in temperate and colder climates, these industrial concrete floors can be susceptible to freezing, which can cause them to crack and become damaged. To prevent these problems, it is important to take the proper preventative measures. In this article, we will discuss several effective methods for protecting industrial concrete floors from freezing.
One of the most effective ways to protect concrete from freezing is to use penetrating sealants. These substances penetrate deep into the pores of the concrete, creating a barrier that prevents water from getting in. This means that even if the concrete is exposed to moisture, it will not freeze inside the structure.
Another solution is to cover the surface of the industrial floor with special coatings or resin floors, which create an impermeable protective layer. These coatings can also be resistant to chemicals, which further increases their functionality in industrial conditions.
Installing heating systems under the concrete floor can effectively combat freezing. Floor heating ensures that the temperature of the industrial concrete floor remains above freezing point. There are various technologies to choose from, such as electric heating, water heating mats or radiant heating.
Floor insulation is another key element. Insulating polystyrene or polyurethane boards installed under concrete can prevent heat loss, thereby maintaining a stable temperature.
Moisture is a major factor in the freezing of industrial floors. Installing drainage systems, such as drains or water channels, can effectively reduce moisture levels. This prevents water from entering the pores of the concrete, minimizing the risk of freezing. After exposure to water, floor repairs are often necessary.
Inside industrial buildings, it is worth investing in air conditioning systems and dehumidifiers that will control humidity levels. Maintaining the indoor air at the right humidity level protects industrial concrete floors from excessive water absorption.
During the production of concrete, special additives can be added to increase its resistance to low temperatures and freeze-thaw cycles. Additives such as microspheres, polypropylene fibers or hydrophobic substances help to protect the structure of concrete. If you need concrete pumping, contact us.
Superplasticizers improve the consistency of concrete, which is important when pouring it. Industrial concrete floors with better consistency have smaller pores through which water can penetrate, which reduces the risk of freezing.
Regular inspection of the concrete floor allows for early detection of minor damage or cracks that can lead to more serious problems polished concrete. Any damage should be repaired immediately to prevent further damage.
Keeping the surface of your concrete floor clean minimizes the risk of moisture and chemical build-up that can contribute to freezing. Regular cleaning and maintenance of the surface helps keep it in good condition.
Protecting your industrial concrete floor from freezing is a key element in maintaining its durability and functionality. The use of appropriate sealants, heating systems, moisture control, protective additives and regular maintenance can effectively prevent damage caused by freezing. Investing in these preventative measures pays off in the long term, ensuring the reliability and safety of industrial concrete surfaces.
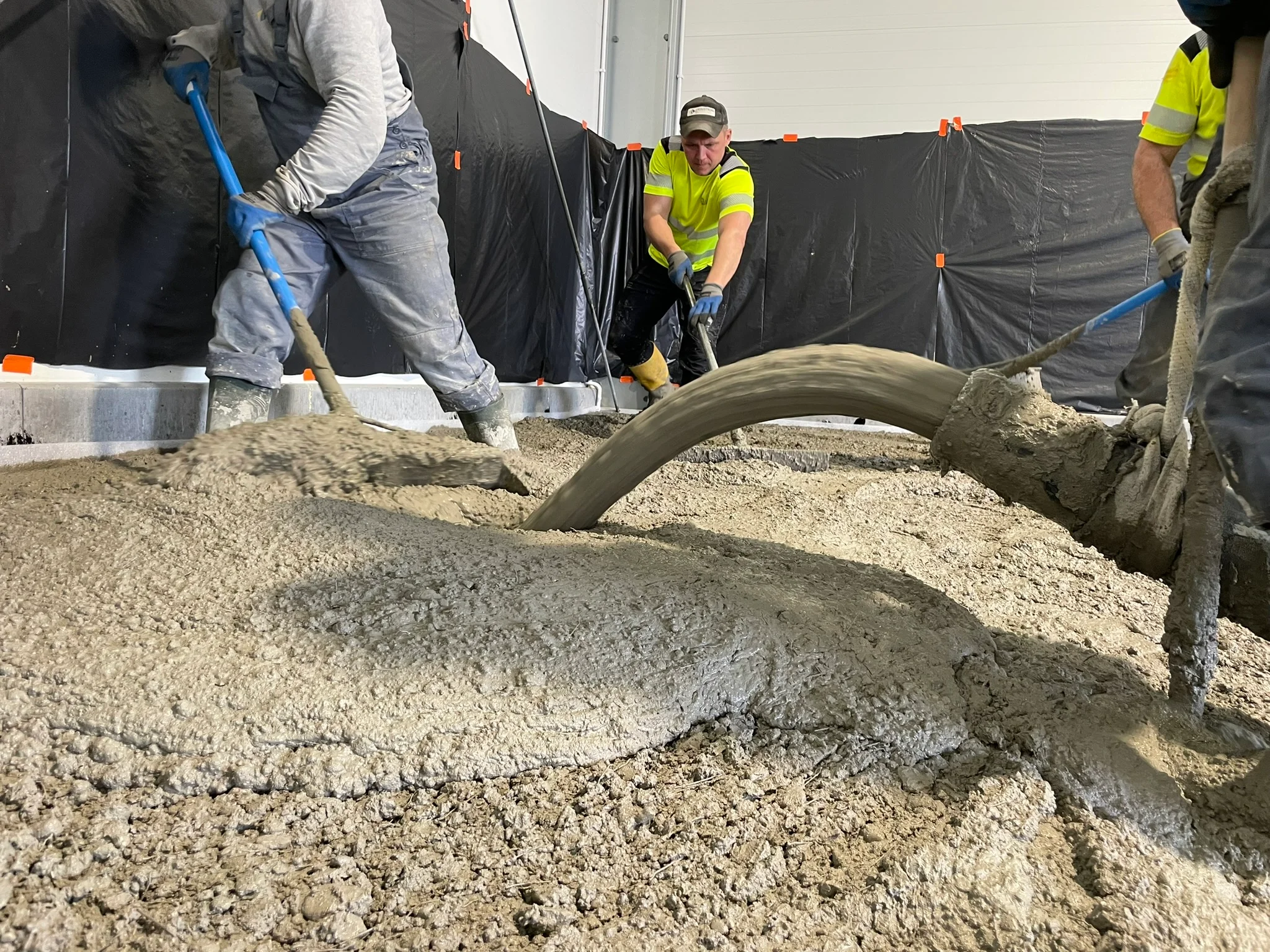
Waterproofing of industrial concrete floor. Basic conditions.
Industrial concrete floors are exposed to many environmental factors such as moisture, chemicals and heavy use, which can lead to degradation.
To increase their durability and functionality, it is crucial to use appropriate waterproofing. In this article, we discuss the basic conditions for effective waterproofing of industrial concrete floor.
The first step in the process of waterproofing a concrete floor is a thorough assessment of the condition of the substrate. Any cracks, gaps, unevenness and signs of moisture or chemical contamination should be identified. It is also necessary to check the strength and cohesion of the concrete.
Before waterproofing begins, the surface of the industrial concrete floor must be thoroughly cleaned of all dirt, grease, oil and loose concrete fragments. The use of appropriate cleaning agents and sandblasting or grinding equipment may be necessary. Any cracks or gaps should be repaired with special repair mortars that are compatible with the waterproofing system being used.
Penetrating sealers, such as silicates or silicates, penetrate deep into the concrete structure, forming water-resistant crystals. They provide long-term protection against moisture and are particularly effective in conditions where water migrates through the pores of the concrete.
Hydrophobic coatings such as polyurethanes, epoxies or acrylics create an impermeable protective layer on the surface of industrial concrete flooring. These products can also be resistant to chemicals, which increases their functionality in industrial conditions.
Hydraulic membranes, especially bituminous membranes, can be used as a protective layer under concrete surfaces. They are flexible and adhere perfectly to the substrate, protecting it from water penetration and protecting walls from impacts safety barriers.
Correct application conditions are crucial for the effectiveness of waterproofing. Temperatures should be above 5°C and relative humidity should be low to ensure proper drying and curing of coatings or membranes.
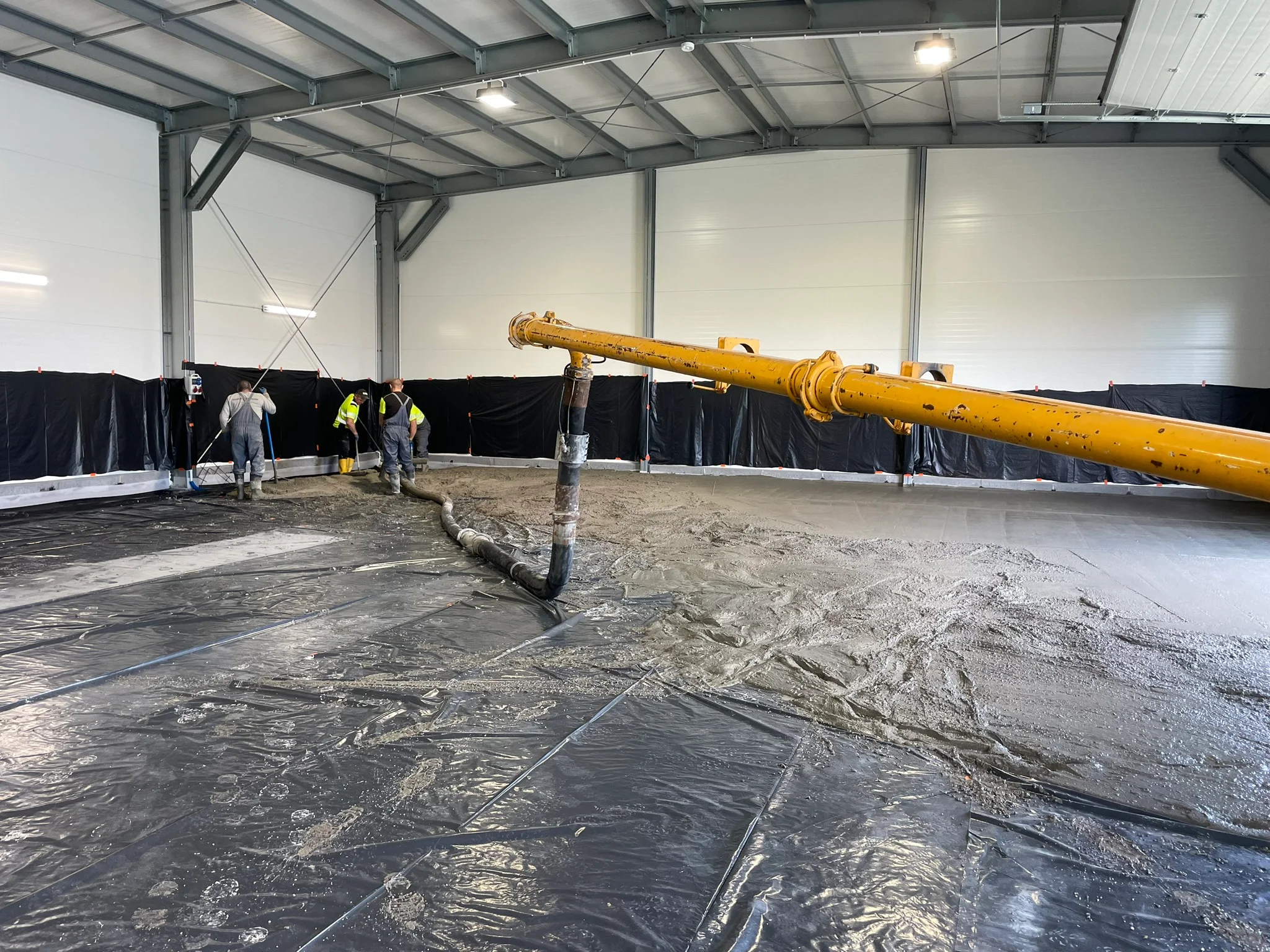
Application techniques may vary depending on the waterproofing system chosen. Penetrating sealants are typically applied using rollers, brushes or sprayers. Industrial concrete floor coatings and membranes may be applied using brushes, rollers or spray methods, depending on the product and the size of the surface. Each coat should be applied evenly and the time between coats should be strictly adhered to according to the manufacturer's instructions.
Once the waterproofing system has been applied to the industrial concrete floor, a thorough visual inspection is essential. Check that the surface is evenly coated and that there are no areas of poor application or damage.
To ensure that waterproofing is effective, concrete water absorption tests can be carried out. This involves the controlled exposure of the surface to water and observing its behavior. In the case of hydrophobic coatings, water droplets should form on the surface without penetrating the concrete.
Regular inspections of the waterproofed surface of the industrial concrete floor are essential to detect any damage or wear of the coating in time. Systematic inspection allows for a quick response and possible repairs, minimizing the risk of more serious problems.
Maintaining cleanliness on the surface of industrial flooring, in particular removing all chemicals, fats and oils, extends the durability of the waterproofing. It is recommended to wash the surface regularly using appropriate cleaning agents.
Effective waterproofing of industrial concrete floor is a key element in ensuring its durability, safety and functionality. Proper preparation of the substrate, selection of the right waterproofing system and precise application and quality control are important. Regular maintenance and inspections allow for maintaining high quality protection for a long time. By taking appropriate measures, the life of the concrete floor can be significantly extended and the risk of damage related to moisture penetration can be minimized.
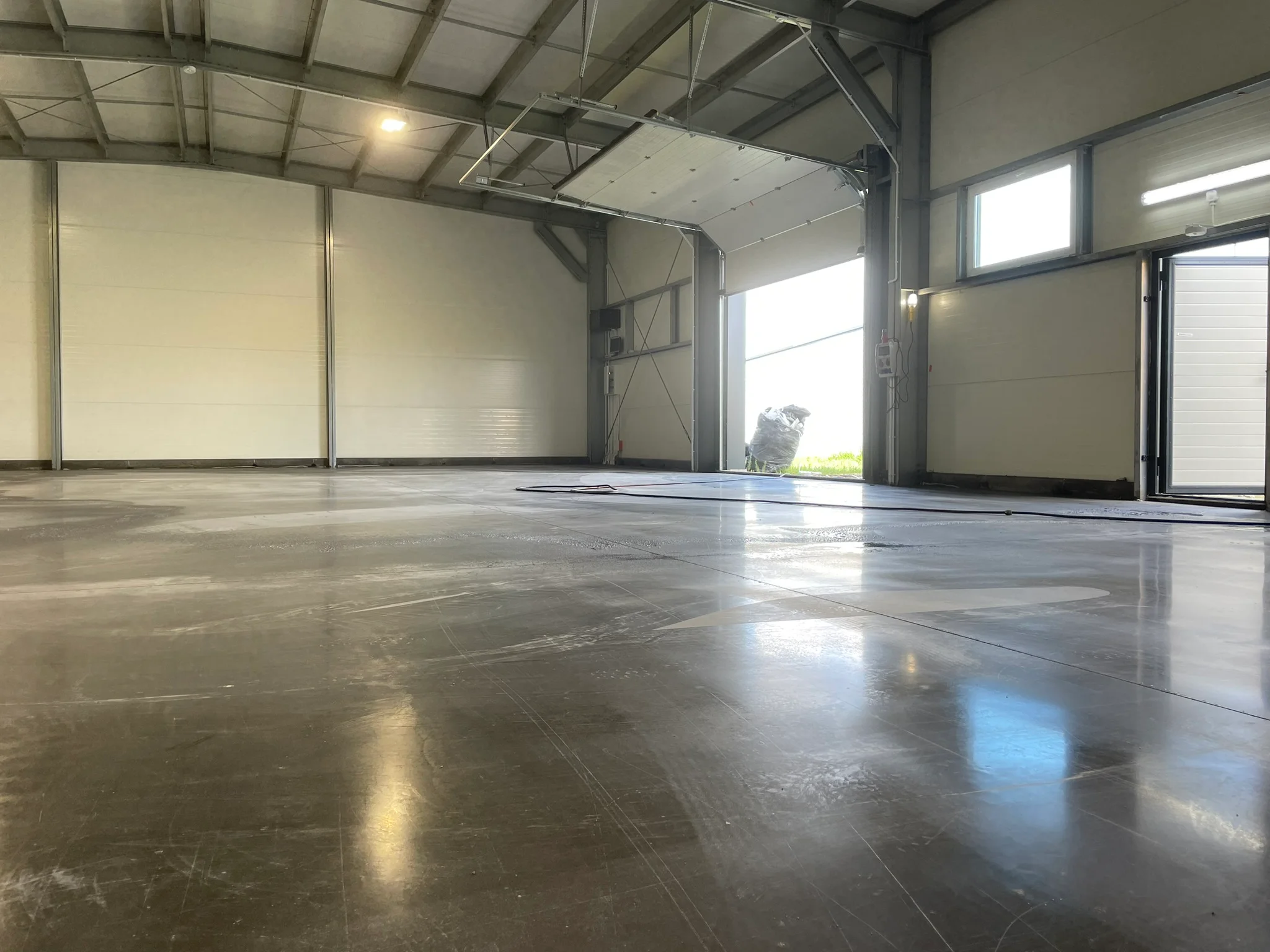
Work results:
- construction of industrial concrete floor - 300 m2.