Where can I order an industrial concrete floor design?
Industrial concrete floors are the foundation of many industrial sectors due to their exceptional strength, durability and resistance to mechanical and chemical loads.
Manufacturing companies, warehouses, logistics distribution centers, and industrial halls use this technology to ensure stability and operational efficiency. But where can you order a professional design for such an industrial floor? Here are a few key places to consider.
Construction companies with extensive experience in the construction of industrial floors often offer a comprehensive service – from design, through material supply, to implementation.
It is worth paying attention to references, previous projects and customer opinions. Companies such as Bautech and Si-Tech have a rich portfolio and are able to provide a project tailored to the individual needs of the investor.
Large design and architectural offices often have specialists in industrial flooring projects on their teams. Engineering offices offer the service of designing concrete industrial floor using the latest technologies and materials. Their competences allow them to develop projects that are not only functional, but also economical to implement.
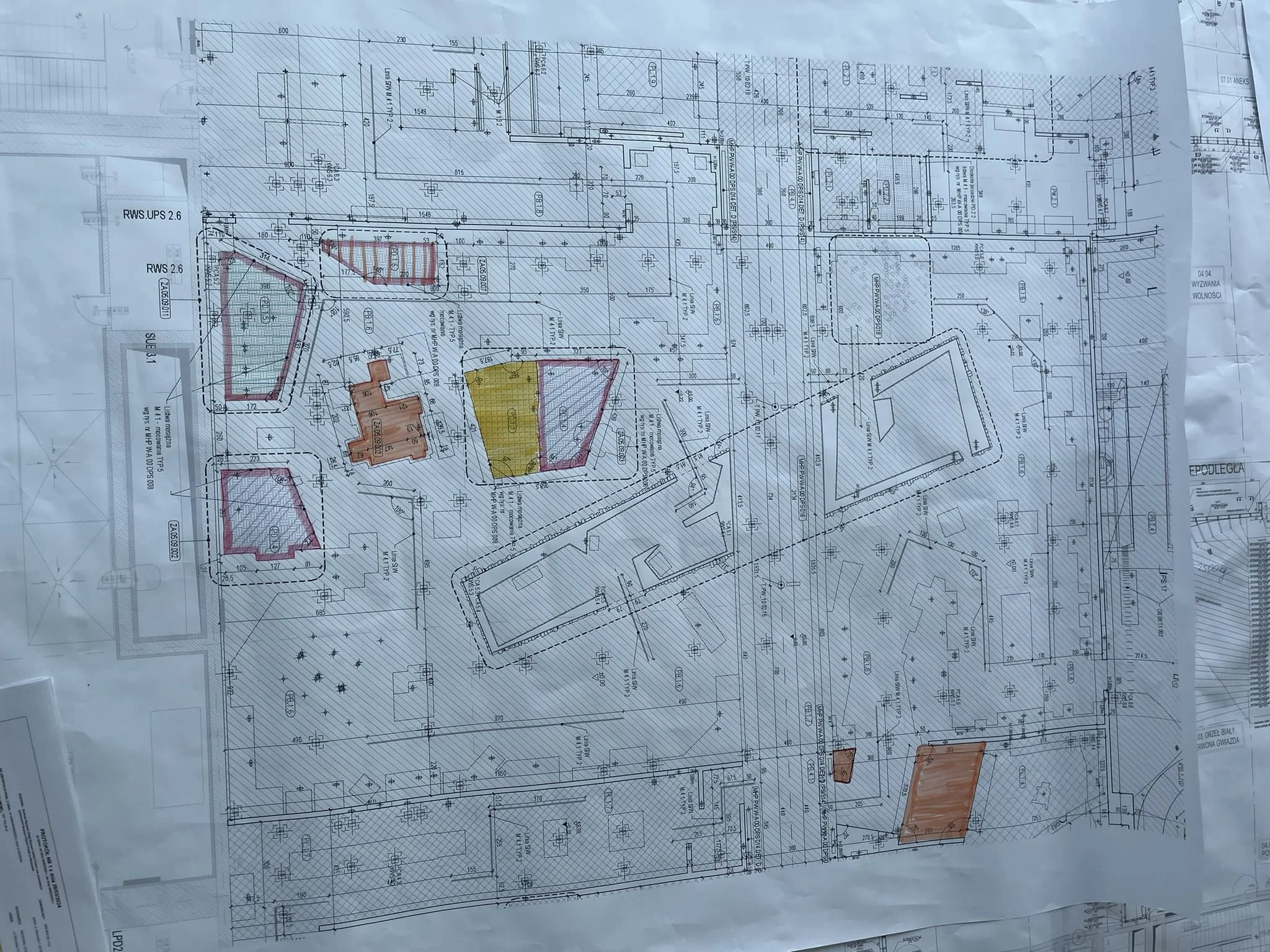
Technical advice is a key element in the process of designing an industrial floor. Companies such as Lafarge Holcim offer consulting services in the selection of appropriate materials, manufacturing technology, and even conduct in-situ research. Thanks to their experience and knowledge of the market, you can obtain a project of the highest quality.
Online design platforms and specialist software such as Autodesk Revit or Tekla Structures offer tools for independent design of industrial floors and resin floors. However, it is worth remembering that using such advanced applications requires appropriate technical knowledge and experience. Therefore, if someone is not confident in their skills, it is better to consult a professional.
Manufacturers of building materials often offer technical support services, including design. Companies such as Sika, Cemex and Heidelberg offer special consulting services in the selection of appropriate concrete mixes and technology for making industrial flooring. Because they have direct access to the latest materials, they can offer the most effective and innovative solutions.
Ordering an industrial concrete floor project requires taking into account many factors: from technical specifications, through the availability of materials, to the implementation and maintenance of the finished floor. Choosing the right contractor or designer is crucial to the success of the entire project. Construction companies, design offices, technical consulting and manufacturers of building materials are the main places where you can order such a project. Regardless of the option chosen, the most important thing is safety, durability and full compliance with the investor's requirements.
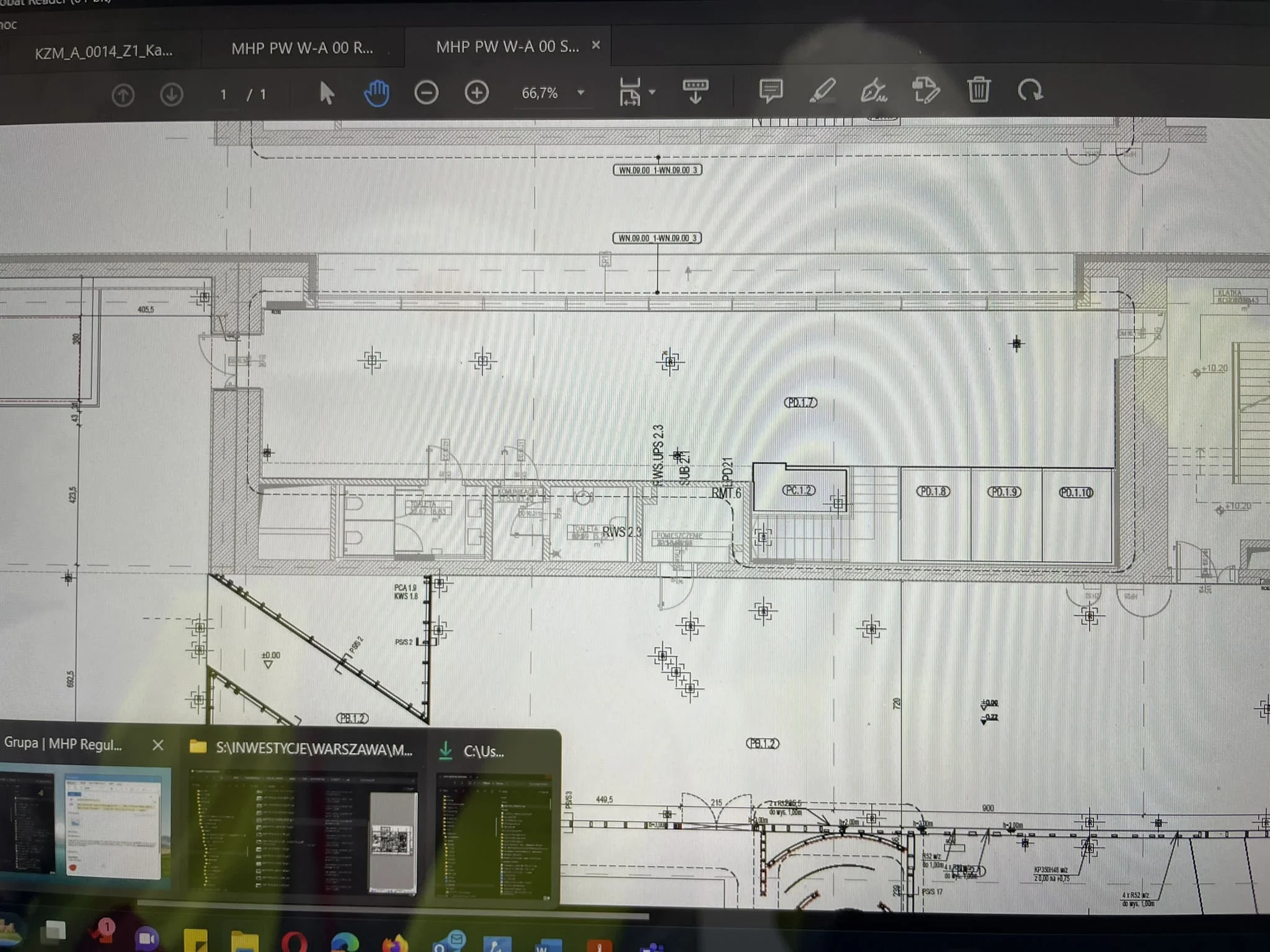
What points should an industrial concrete floor design consist of?
Designing an industrial concrete floor is a complex process that requires taking into account many technical, economic and functional aspects.
Industrial concrete floors are exposed to intense mechanical and chemical loads and variable environmental conditions, which is why each design stage must be precisely defined. In this article, we present the main points that should make up such a design.
The first step in designing an industrial floor is to thoroughly analyze the utility requirements. The following must be taken into account: the type of industrial activity and the specificity of production processes, the type and intensity of traffic (pedestrian, vehicular, warehouse), loads acting on the floor (static and dynamic), hygiene requirements and environmental conditions (chemical, temperature, humidity).
In order to provide proper support for a polished concrete floor, geotechnical soil tests are necessary. They will allow for: assessment of the bearing capacity of the subsoil, determination of the groundwater level, identification of possible problems related to soil stability, formulation of recommendations for substrate preparation.
The substrate and supporting layers are crucial for the durability of the floor. The design of this part of the floor should include: the design of the drainage and base layer, a specification of the materials used to make the supporting layers, a definition of the thickness and method of laying the individual layers, the principles of compaction and testing the quality of the layers made so as not to have to repair the floors.
The concrete mix is the foundation of any industrial floor. This stage of the project should include: determination of the concrete class (compressive strength, bending strength), composition design (proportions of cement, aggregate, water and additives), specification of improving agents (e.g. plasticizers, sealants), requirements for the consistency and workability of concrete.
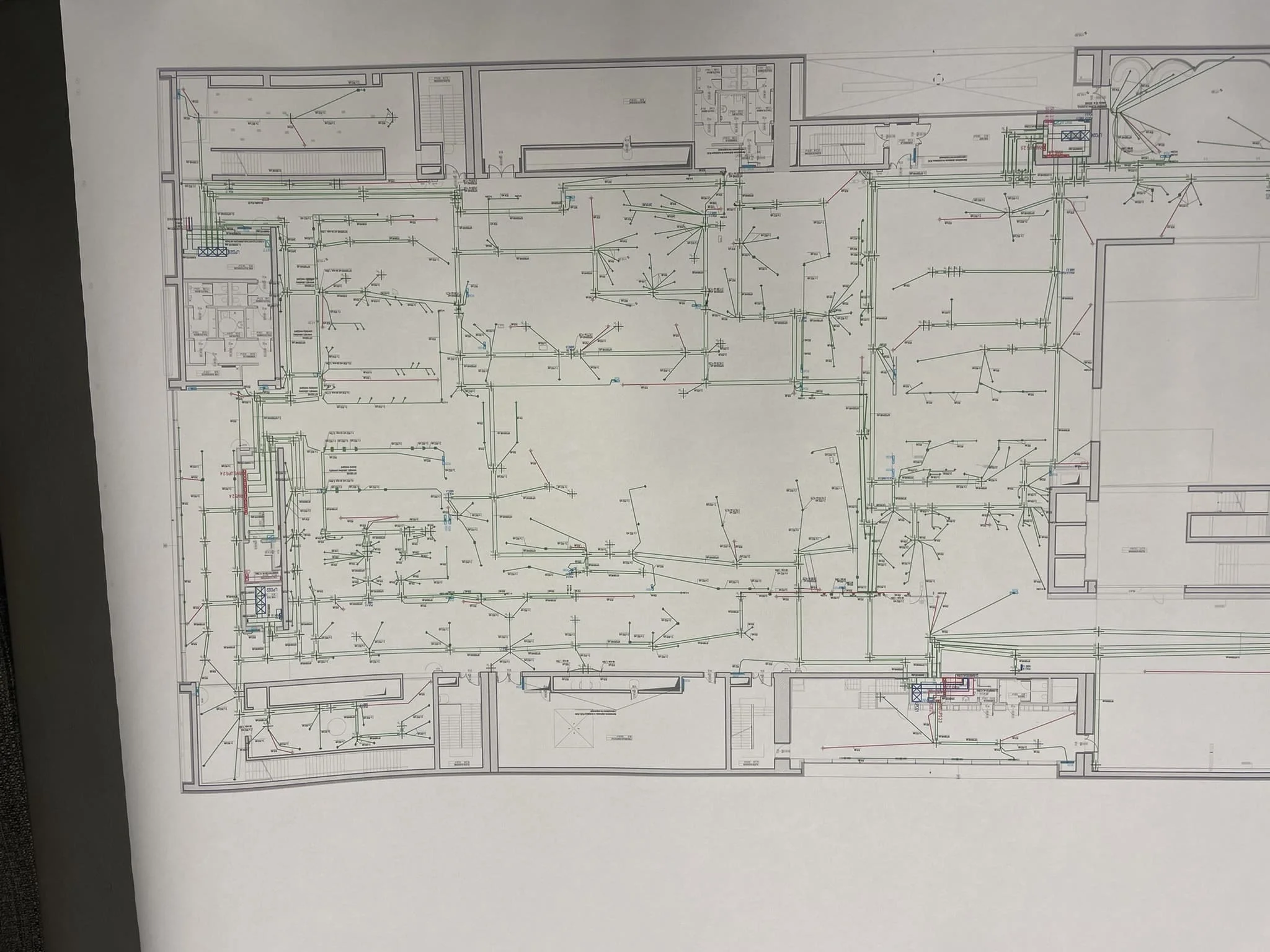
Expansion joints and reinforcement are essential for controlling concrete shrinkage and transferring loads. The design should include: types and arrangement of reinforcing bars or mesh, determination of locations and details of expansion joints (shrinkage, insulation, structural), recommendations for installation of reinforcement and expansion joints.
Proper concrete pumping and maintenance are crucial to its durability. The project should include: methods of placing and compacting concrete, surface finishing techniques (e.g. grinding, polishing), methods of concrete maintenance (maintaining humidity, protection against excessive evaporation).
Depending on the usage requirements, industrial floors may require additional protective coatings. The design should include: types of coatings (e.g. epoxy, polyurethane), application methods and technical specifications, recommendations for maintenance and cleaning of coatings.
The final, but no less important element of the project is the quality control and work acceptance procedure, including: the schedule and scope of quality controls (e.g. strength tests, surface evenness), requirements for technical documentation, safety (e.g. safety barriers) and acceptance of individual stages, final investment acceptance protocol.
Industrial concrete floor project is a comprehensive document, requiring a detailed approach to each stage of implementation. From the analysis of utility requirements, through preparation of the substrate, to execution and final acceptance - each step must be well thought out and well documented. Thanks to this, the floor will serve for many years, maintaining its functional and durability properties. Choosing proven designers and contractors minimizes the risk of problems and maximizes the effectiveness of the investment.